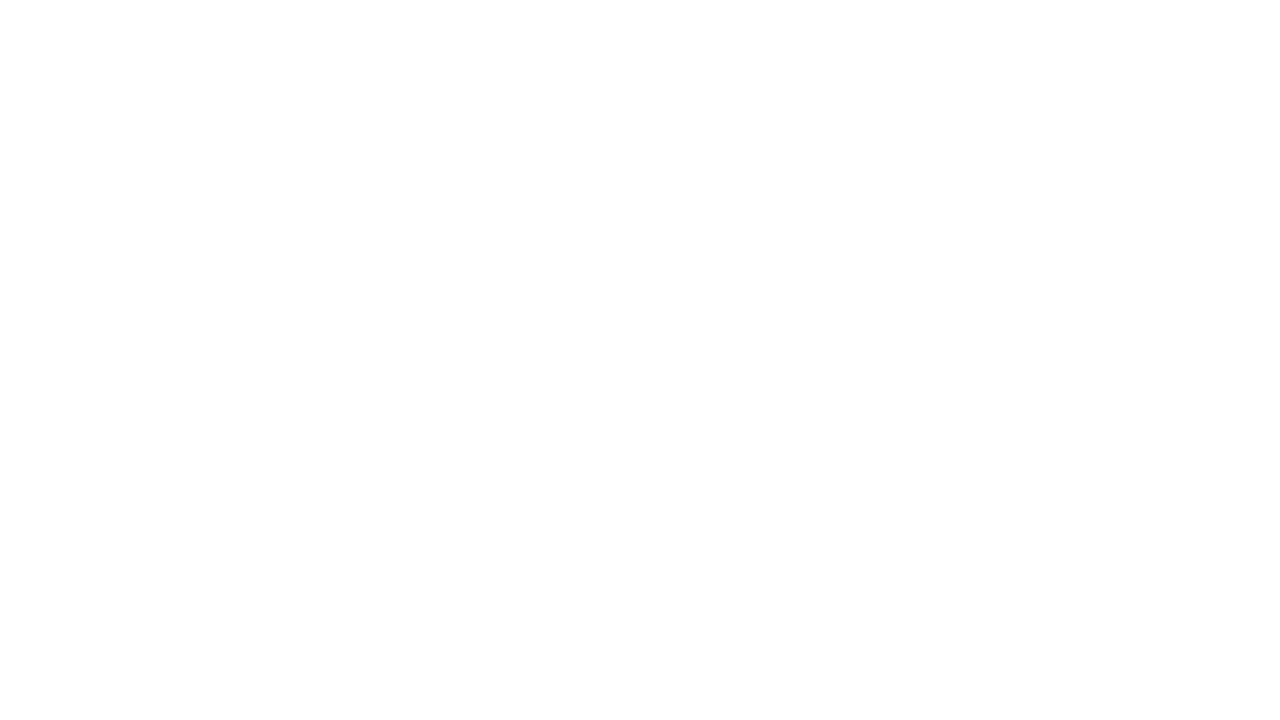
Aluminum engine parts are prone to oxidation over time due to exposure to air, moisture, and high temperatures. This oxidation can lead to a buildup of a dull, chalky coating on the surface of the parts, which can affect their appearance and potentially their performance. Cleaning oxidized aluminum engine parts is an important maintenance task to keep your engine running smoothly and looking its best.
Before we dive into the cleaning process, it's crucial to understand what causes oxidation on aluminum engine parts. Aluminum naturally forms a thin oxide layer when exposed to air, acting as a protective barrier against further oxidation. However, certain factors can cause this oxide layer to thicken and become unsightly.
Causes of Oxidation | Description |
---|---|
Exposure to Air and Moisture | Prolonged exposure to moisture can cause the oxide layer to thicken and become powdery or crusty. |
Salt Exposure | Road salt used for de-icing can accelerate the oxidation process on aluminum engine components. The salt reacts with the aluminum oxide layer, causing further corrosion. |
Battery Acid Vapors | The sulfuric acid vapors from the vehicle's lead-acid battery can contribute to aluminum oxidation, especially on nearby components. |
The first step in addressing oxidation is to visually inspect your engine bay. Look for the following signs:
White, powdery deposits or crusty buildup on aluminum components like the intake manifold, valve covers, or engine block itself.
Discoloration or pitting on the aluminum surface, which can indicate advanced oxidation.
Pay close attention to areas around the battery, as the sulfuric acid vapors can accelerate the oxidation process.
If you catch the oxidation early, a simple cleaning routine can work wonders. Follow these steps for mild cases:
Use a mild detergent or aluminum cleaner and a soft-bristle brush to gently scrub the affected areas.
Avoid abrasive cleaners that can scratch the surface and potentially cause further damage.
Rinse the area thoroughly with water and dry it completely.
Apply a metal polish or protectant specifically designed for aluminum to restore the shine and provide a protective coating.
For those stubborn cases of oxidation that won't budge with mild cleaners, more aggressive methods are required. Here's how to tackle heavy oxidation:
Use a diluted acid solution, like vinegar or a mild muriatic acid (hydrochloric acid) mixture. Exercise caution and proper safety precautions when working with acids, and always follow the manufacturer's instructions.
Soak or spray the affected area with the acid solution, letting it sit briefly to work its magic.
Scrub the area with a brush and rinse thoroughly with water.
Neutralize any remaining acid by creating a baking soda and water solution and applying it to the cleaned surface.
In extreme cases of heavy oxidation, you may need to consider media blasting, such as bead blasting, for parts that can be easily removed from the engine. This process involves propelling small, abrasive particles at high velocity to remove the oxidation layer.
Media Blasting Types | Description |
---|---|
Bead Blasting | Small glass or ceramic beads are propelled at high velocity to remove the oxidation layer. |
Sand Blasting | Fine sand particles are used as the abrasive media, providing a more aggressive cleaning action. |
Soda Blasting | Baking soda is used as the abrasive media, offering a gentler cleaning option for delicate surfaces. |
Once you've successfully cleaned the oxidized aluminum engine parts, it's crucial to take preventative measures to avoid future buildup.
Apply a corrosion-inhibiting coating or sealant specifically designed for aluminum to protect the cleaned surfaces.
Regular maintenance is key. Make it a habit to clean and dry the engine bay regularly, removing any moisture or contaminants that could contribute to oxidation.
If you live in an area with heavy road salt usage during winter, frequently rinse the undercarriage and engine bay to remove salt buildup.
For added protection around the battery area, consider using a battery corrosion preventative product. These products help neutralize the acidic vapors that can accelerate oxidation on nearby aluminum components.
Preventative Products | Description |
---|---|
Corrosion-Inhibiting Coatings | These coatings form a protective barrier against moisture and contaminants, preventing oxidation. |
Battery Corrosion Preventatives | Neutralize acidic vapors from the battery, protecting nearby aluminum components. |
Engine Bay Dressings | Some dressings contain corrosion inhibitors and can help protect aluminum surfaces. |
The cost of cleaning and protecting oxidized aluminum engine parts can vary depending on the severity of the oxidation and the methods used.
Mild detergents, brushes, and polishes typically range from $10 to $30.
Acid-based cleaners like muriatic acid can cost between $10 and $20.
Professional media blasting services can range from $50 to $200, depending on the number of parts involved.
Corrosion-inhibiting coatings or sealants can range from $15 to $50.
It's generally more cost-effective to address oxidation issues early before they become severe. Regular maintenance and preventative measures can help minimize long-term costs and potentially save you from having to replace heavily oxidized parts.
Oxidation on aluminum engine parts is a common issue, but with the right knowledge and techniques, it's a problem that can be easily tackled. By understanding the causes, inspecting your engine bay regularly, and employing the appropriate cleaning methods, you can keep your vehicle's aluminum components looking their best and functioning optimally.
Remember, prevention is key. Implementing regular maintenance routines and using corrosion-inhibiting products can go a long way in minimizing future oxidation buildup. With a little elbow grease and the right approach, you can keep your ride looking sharp and running smoothly for years to come.
Here is an FAQ section with 10 additional questions and answers based on the article content:
The white powdery buildup is aluminum oxide, formed when aluminum is exposed to air and moisture over time. This oxidation process creates a crusty layer on the surface of the aluminum.
While oxidation is primarily a cosmetic issue, severe cases can lead to pitting and degradation of the aluminum surface if left unchecked for too long.
Look for white or gray powdery deposits, discoloration, or pitting on aluminum components like the intake manifold, valve covers, or engine block itself.
For mild cases, use a soft-bristle brush and a mild detergent or aluminum cleaner, then rinse thoroughly and apply a metal polish or protectant.
Diluted acid solutions like vinegar or muriatic acid can help remove stubborn oxidation when scrubbed onto the affected area. Proper safety precautions are essential.
Media blasting involves propelling abrasive particles at high velocity to remove heavy oxidation layers. It may be required for extreme cases on removable parts.
Apply a corrosion-inhibiting coating or sealant designed for aluminum, and regularly clean and dry the engine bay to remove moisture and contaminants.
Yes, the sulfuric acid vapors from lead-acid batteries can accelerate oxidation on nearby aluminum components. Consider using battery corrosion preventative products.
Costs can range from $10-$30 for mild cases to $50-$200 for professional media blasting services, plus the cost of coatings or sealants.
It's generally more cost-effective and easier to address oxidation issues early before they become severe. Regular maintenance can prevent the need for more extensive repairs or replacements.
Sarah isn't your average gearhead. With a double major in Mechanical Engineering and Automotive Technology, she dived straight into the world of car repair. After 15 years of turning wrenches at dealerships and independent shops, Sarah joined MICDOT to share her expertise and passion for making cars run like new. Her in-depth knowledge and knack for explaining complex issues in simple terms make her a valuable asset to our team.