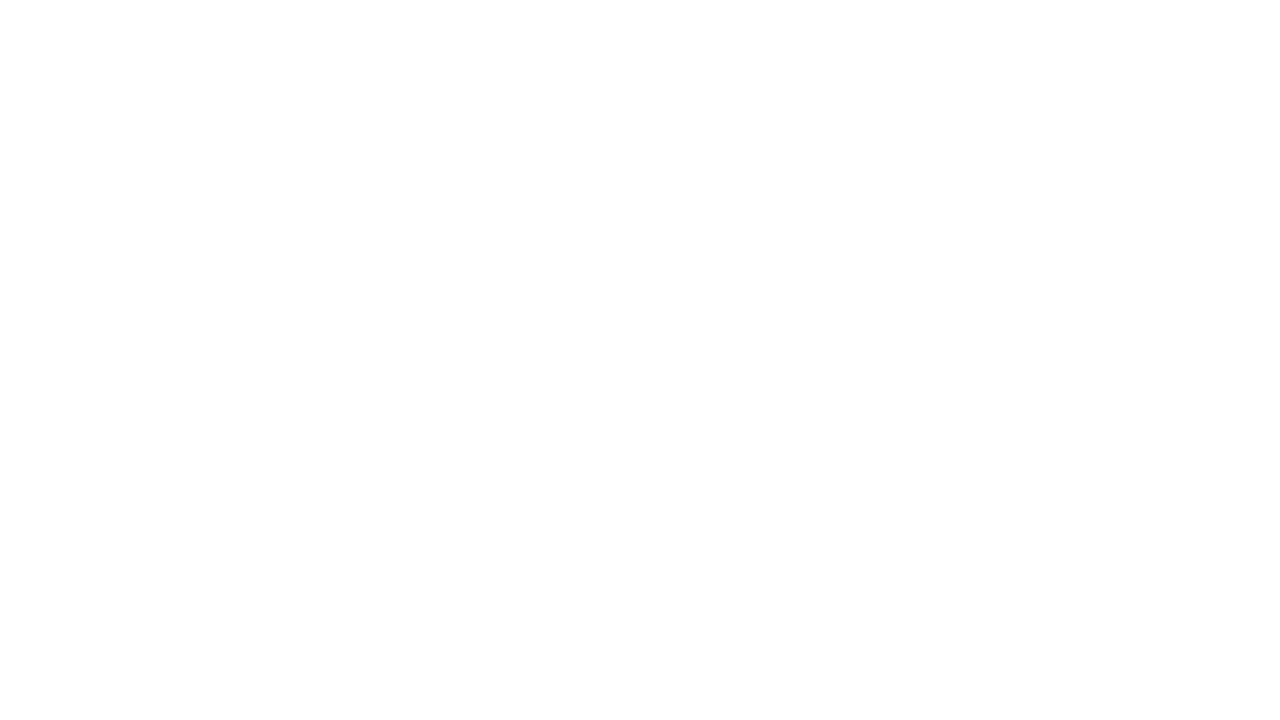
In the ever-evolving automotive industry, predictive maintenance powered by machine learning is a game-changer. This cutting-edge approach empowers manufacturers and service providers to proactively identify potential failures, minimizing costly downtime and ensuring optimal vehicle performance. By harnessing the power of data and advanced algorithms, predictive maintenance revolutionizes asset management, maximizing operational efficiency and enhancing customer satisfaction.
Traditionally, maintenance strategies have been reactive, addressing issues only after failures occur, or preventive, based on predetermined schedules. However, as vehicles become increasingly complex, these approaches are no longer sufficient to ensure reliability and optimal performance. Predictive maintenance addresses this challenge by leveraging advanced sensors, data analytics, and machine learning algorithms to continuously monitor asset health and predict potential failures before they escalate.
Predictive maintenance relies on two main machine learning approaches: supervised and unsupervised learning.
Supervised Learning | Unsupervised Learning |
---|---|
Trained on labeled data | Identifies patterns in unlabeled data |
Used for predictive modeling | Used for anomaly detection and clustering |
Algorithms: Random Forests, Support Vector Machines, Neural Networks | Algorithms: Clustering, Anomaly Detection |
Supervised learning algorithms learn from labeled historical data, enabling them to make predictions on new, unseen data. Common algorithms include:
Random Forests: Ensemble learning methods that combine multiple decision trees for improved accuracy and robustness.
Support Vector Machines (SVMs): Powerful algorithms for classification and regression tasks, suitable for fault detection and remaining useful life estimation.
Neural Networks: Inspired by the human brain, these algorithms excel at recognizing patterns in complex, non-linear data, making them valuable for time-series forecasting and predictive modeling.
Unsupervised learning algorithms identify patterns and relationships in unlabeled data, making them valuable for anomaly detection and clustering tasks. Key algorithms include:
Clustering: Groups similar data points together based on their characteristics, enabling the identification of different operating modes or asset segmentation.
Anomaly Detection: Identifies data points or patterns that deviate significantly from expected behavior, detecting early signs of equipment degradation or sensor faults.
Predictive maintenance relies on various data sources, including:
Sensor Data: Measurements from sensors monitoring critical components, such as temperature, vibration, pressure, and voltage.
Historical Maintenance Records: Insights into past failures, repairs, and maintenance activities, enabling pattern recognition and root cause analysis.
Operational Parameters: Vehicle usage patterns, driving conditions, and environmental factors that may influence asset degradation.
Data preprocessing techniques, such as filtering, interpolation, and normalization, are applied to clean and format the raw data, ensuring its quality and suitability for analysis.
Feature Engineering | Model Training |
---|---|
Selecting and transforming relevant features | Choosing appropriate algorithms |
Dimensionality reduction, feature selection, construction | Splitting data into training and validation sets |
Creating meaningful inputs for models | Adjusting model parameters to minimize prediction error |
Feature engineering extracts relevant features from the collected data, creating meaningful inputs for machine learning models. Model selection considers factors such as data complexity and desired output (classification, regression, or anomaly detection). During training, models learn patterns and relationships from the training data, while validation techniques assess their performance and generalization capabilities.
Once trained and validated, predictive maintenance models are deployed to continuously monitor incoming data streams. These models analyze the data and provide predictions or alerts about potential failures, remaining useful life estimates, or anomalous behavior.
Based on these predictions, maintenance teams can proactively plan and schedule maintenance activities, order replacement parts, or take corrective actions to prevent failures and minimize downtime. Effective maintenance planning ensures efficient resource allocation and optimal timing for maintenance activities, maximizing asset availability and operational efficiency.
Reduced vehicle downtime and associated costs
Extended lifespan of vehicle components and systems
Optimized maintenance scheduling and resource allocation
Improved vehicle reliability and performance
Enhanced safety through early detection of potential issues
Increased customer satisfaction and brand loyalty
Competitive advantage through efficient asset management
Reduced environmental impact through optimized maintenance practices
Data-driven decision-making for maintenance operations
Continuous improvement through model updates and retraining
Machine learning has revolutionized predictive maintenance in the automotive industry, enabling proactive identification of potential failures and timely interventions. By leveraging advanced algorithms, sensor data, and historical records, predictive maintenance models can accurately predict asset degradation, optimize maintenance schedules, and minimize unplanned downtime. As the industry continues to embrace this data-driven approach, the benefits of increased operational efficiency, extended asset lifespan, and enhanced customer satisfaction will drive further adoption and innovation in this field.
Predictive maintenance powered by machine learning offers several key benefits, including reduced vehicle downtime, extended component lifespan, optimized maintenance scheduling, improved reliability and safety, increased customer satisfaction, and competitive advantage through efficient asset management.
Supervised learning algorithms, such as random forests, support vector machines, and neural networks, are trained on labeled historical data to make predictions on new, unseen data, enabling accurate predictive modeling and remaining useful life estimation for vehicle components and systems.
Unsupervised learning algorithms, like clustering and anomaly detection, identify patterns and anomalies in unlabeled data, enabling the detection of early signs of equipment degradation, sensor faults, and different operating modes without relying on labeled training data.
The main data sources for predictive maintenance models include sensor data monitoring critical components, historical maintenance records providing insights into past failures and repairs, and operational parameters such as vehicle usage patterns and environmental conditions.
Feature engineering involves selecting, transforming, and constructing relevant features from the collected data, creating meaningful inputs for machine learning models, enabling them to learn patterns and relationships more effectively and make accurate predictions.
Trained and validated predictive maintenance models are deployed to continuously monitor incoming data streams, analyze the data, and provide predictions or alerts about potential failures, remaining useful life estimates, or anomalous behavior, enabling maintenance teams to proactively plan and schedule maintenance activities.
By providing accurate predictions of potential failures and remaining useful life estimates, predictive maintenance models enable maintenance teams to optimize maintenance scheduling, ensuring efficient resource allocation and optimal timing for maintenance activities, maximizing asset availability and operational efficiency.
Predictive maintenance can reduce environmental impact by optimizing maintenance practices, minimizing unnecessary maintenance activities, and extending the lifespan of vehicle components and systems, leading to reduced waste and resource consumption.
By improving vehicle reliability, performance, and uptime, predictive maintenance can enhance customer satisfaction and brand loyalty, as customers experience fewer disruptions and enjoy a better overall ownership experience with the vehicles.
Predictive maintenance models can be continuously improved through model updates and retraining, incorporating new data and insights, enabling organizations to adapt to changing conditions and further refine their maintenance strategies for optimal performance and efficiency.
Miguel started tinkering with car radios as a teenager, fascinated by the intricate dance of wires and circuits. This passion led him to pursue a career as an automotive electrician. For the past 10 years, Miguel has tackled everything from flickering headlights to mysterious electrical gremlins. He thrives on troubleshooting electrical problems and enjoys sharing his knowledge to empower car owners to understand their vehicles better.