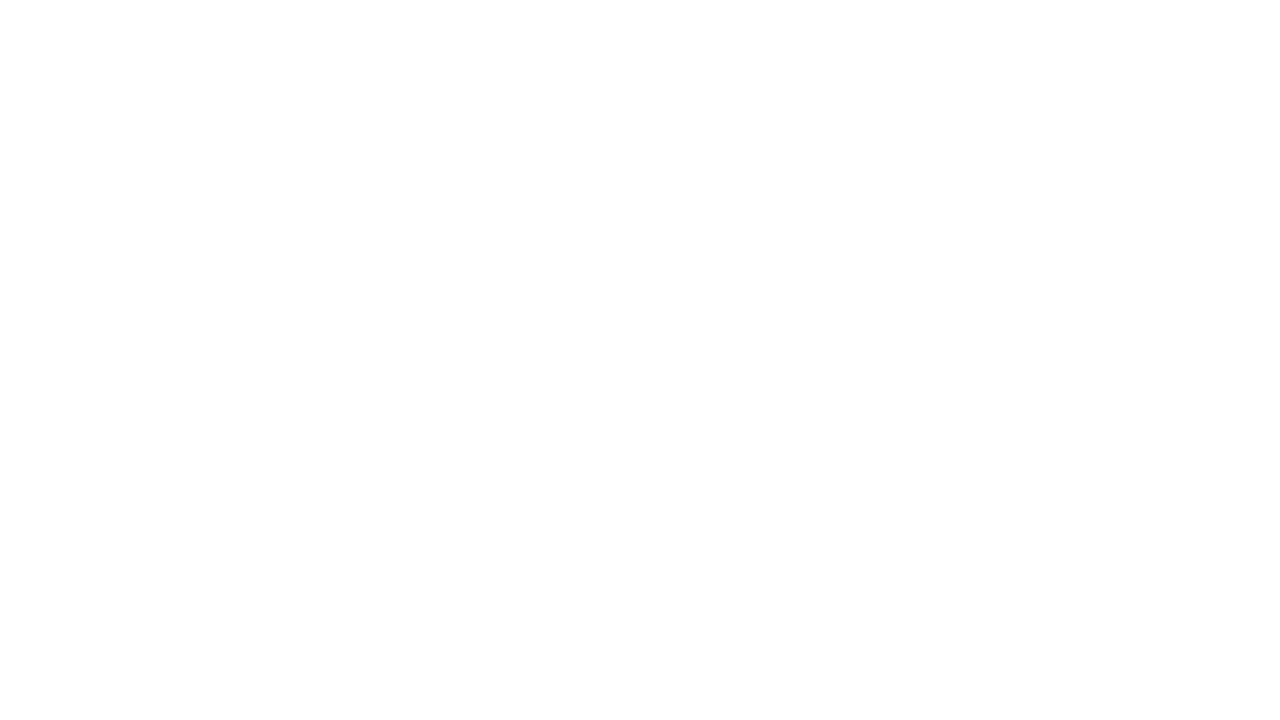
The diagnostic trouble code (DTC) P03A2 stands for "Cylinder 2 Pressure Sensor Circuit High". This code indicates that the engine control module (ECM) has detected an abnormally high voltage signal from the cylinder 2 pressure sensor circuit.
Before we dive into the nitty-gritty details, let's first explore the primary suspects behind this pesky code. The P03A2 code, which stands for "Cylinder 2 Pressure Sensor Circuit High," can typically be attributed to one of the following main causes:
Cause | Description |
---|---|
Faulty Pressure Sensor | The cylinder 2 pressure sensor itself can fail due to mechanical wear, contamination, or internal damage, causing it to provide incorrect readings or short circuit internally. |
Wiring Issues | Problems like damaged wires, loose connectors, corrosion, or shorts to ground/voltage in the wiring harness connecting the pressure sensor to the engine control module (ECM) can trigger this code. |
Short Circuit to Voltage | If the signal wire from the pressure sensor gets shorted to a power source, it will cause excessively high voltage readings, setting off the "circuit high" code. |
Just like any other component in your vehicle, the cylinder 2 pressure sensor is susceptible to wear and tear. Over time, it can fall victim to mechanical wear, contamination, or internal damage, causing it to provide incorrect readings or even short circuit internally. This faulty behavior can trigger the P03A2 code, leaving you scratching your head.
In some cases, the pressure sensor may fail due to exposure to extreme temperatures, vibrations, or contaminants like oil or debris. Additionally, manufacturing defects or improper installation can also contribute to premature sensor failure.
Ah, the age-old nemesis of every mechanic – wiring issues! Problems like damaged wires, loose connectors, corrosion, or shorts to ground or voltage in the wiring harness connecting the pressure sensor to the engine control module (ECM) can also be the root cause of this code. These pesky wiring gremlins can wreak havoc on your vehicle's electrical system, leading to all sorts of diagnostic headaches.
Wiring issues can arise due to various factors, including:
Physical damage from rubbing against sharp edges or exposure to heat sources
Corrosion caused by moisture or chemical exposure
Improper installation or routing of the wiring harness
Vibration or stress on the wires over time
Last but not least, we have the dreaded short circuit to voltage. If the signal wire from the pressure sensor gets shorted to a power source, it will cause excessively high voltage readings, setting off the "circuit high" code like a blaring alarm. This scenario can be particularly tricky to diagnose, as it may involve tracking down the source of the short circuit in the wiring harness.
Short circuits to voltage can occur due to various reasons, including:
Chafed or damaged wiring insulation
Pinched or crushed wires
Improper wire routing near power sources
Faulty electrical components or connectors
Now that we've identified the potential culprits, it's time to put on our detective hats and dive into the diagnostic process. Here are the steps I typically follow when tackling the P03A2 code:
Check for Related Codes
Before we get too deep into the weeds, it's always a good idea to check for any other stored codes related to pressure sensors, glow plugs, or wiring faults. These additional codes can provide valuable clues and help us paint a clearer picture of the underlying issue.
Visual Inspection
Next up, it's time for a good old-fashioned visual inspection. I'll carefully examine the wiring harness and connectors for the cylinder 2 pressure sensor, looking for any signs of damage, corrosion, or loose connections. Sometimes, the culprit can be as simple as a frayed wire or a loose connector.
During the visual inspection, pay close attention to:
Exposed or chafed wires
Corroded or damaged connectors
Improper wire routing or securement
Signs of moisture or chemical exposure
Live Data Stream Analysis
With the help of a trusty scanner, I'll dive into the live data stream for the cylinder 2 pressure sensor readings. Abnormal or erratic values can be a telltale sign of a faulty sensor, helping us narrow down the root cause.
| Sensor Reading | Possible Cause | |----------------|-----------------| | Excessively High | Short circuit to voltage, faulty sensor | | Erratic or Fluctuating | Wiring issues, loose connections | | Stuck or Unchanging | Faulty sensor, wiring open circuit |
Resistance Tests
If the visual inspection and live data stream don't reveal the culprit, it's time to break out the multimeter and perform some resistance tests. By checking the resistance values of the pressure sensor and its wiring against the manufacturer's specifications, we can identify any shorts, opens, or out-of-range values that could be causing the P03A2 code.
Resistance tests should be performed with the sensor disconnected and the ignition off
Compare the measured values to the manufacturer's specifications for the specific sensor and wiring
Out-of-range values may indicate a faulty sensor or wiring issue
Once we've identified the root cause, it's time to roll up our sleeves and get to work on the repair. Here's a breakdown of the typical repair procedures for each of the main causes:
If the pressure sensor itself is the culprit, the repair process involves carefully removing the glow plug/pressure sensor assembly for cylinder 2 and replacing it with a new, genuine pressure sensor. Proper seating and torque specifications are crucial to ensure a successful repair.
Follow the manufacturer's recommended procedure for removing and installing the pressure sensor
Use only OEM or high-quality aftermarket sensors to ensure compatibility and longevity
Ensure proper sealing and torque specifications are followed during installation
Perform any necessary post-installation steps, such as bleeding the system or resetting the ECM
In the case of wiring issues, the repair process involves locating and repairing any damaged, shorted, or disconnected wiring. This may involve replacing corroded connectors or entire sections of the wiring harness. Proper wire routing and protection from heat sources and debris are essential to prevent future issues.
Locate and repair or replace any damaged, shorted, or disconnected wiring
Use appropriate wire gauge and insulation for the application
Ensure proper wire routing and securement, away from heat sources and potential chafe points
Replace any corroded or damaged connectors with high-quality replacements
If a short circuit to voltage is the root cause, the repair process involves locating and repairing the short circuit in the pressure sensor wiring. This can be a tedious process, as it may involve inspecting all potential power sources near the wiring for potential short points.
Carefully inspect the entire wiring harness for any signs of chafing, pinching, or damage
Check for potential short points near power sources or other electrical components
Repair or replace any damaged wiring sections or connectors
Ensure proper wire routing and protection after the repair
While repairs are essential, prevention is equally important. Here are some tips to help prevent the P03A2 code from rearing its ugly head again:
Adhering to the manufacturer's recommended maintenance schedule for inspecting and replacing pressure sensors can go a long way in preventing premature failures and costly repairs.
Follow the recommended service intervals for pressure sensor replacement
Inspect sensors during routine maintenance for signs of wear or damage
Replace sensors proactively if they are approaching the end of their service life
During any repair or maintenance work, it's crucial to ensure proper wire routing and protection from heat sources and debris. This simple step can significantly extend the lifespan of your vehicle's wiring harnesses and prevent future issues.
Route wires away from potential chafe points or heat sources
Use appropriate wire loom or conduit for protection
Secure wires properly to prevent excessive movement or strain
When it comes to replacing components like pressure sensors or connectors, it's always best to use genuine OEM (Original Equipment Manufacturer) quality parts. While aftermarket alternatives may be tempting from a cost perspective, they may not always meet the same quality standards, potentially leading to premature failures.
Use OEM or high-quality aftermarket sensors and connectors
Avoid using low-quality or counterfeit parts, as they may fail prematurely
Follow the manufacturer's recommended replacement procedures and specifications
Of course, no discussion about automotive repairs would be complete without addressing the ever-present question of cost. The expenses associated with diagnosing and repairing the P03A2 code can vary significantly depending on the root cause, the vehicle's make and model, and the labor rates at the repair facility.
Repair Type | Typical Cost Range |
---|---|
Pressure Sensor Replacement | $100 - $300 for OEM part + 1-2 hours labor |
Wiring Repair | $50 - $200 for parts like connectors, wiring sections + 1-3 hours labor |
Diagnosis Time | 1-2 hours labor for testing and inspections |
It's important to keep in mind that these are rough estimates, and actual costs may vary based on your specific situation and location. Additionally, some repair facilities may charge additional fees for diagnostic time or shop supplies.
Well, there you have it, folks! We've taken a deep dive into the world of the P03A2 code, exploring its causes, diagnostic procedures, repair methods, and preventive measures. While this code may seem daunting at first, with the right knowledge and approach, it can be tackled head-on.
Remember, a well-maintained vehicle and a keen eye for potential issues can go a long way in preventing costly repairs down the line. By following the recommended maintenance schedules, using high-quality components, and ensuring proper wire routing and protection, you can significantly reduce the likelihood of encountering the P03A2 code or other related issues.
So, keep those wrenches handy, and don't hesitate to seek professional assistance when needed. Happy motoring, and may the diagnostic codes be ever in your favor!
The P03A2 code stands for "Cylinder 2 Pressure Sensor Circuit High." It indicates an issue with the pressure sensor circuit for the second cylinder, typically caused by a faulty sensor, wiring problems, or a short circuit to voltage.
You can identify a faulty pressure sensor by checking the live data stream for abnormal or erratic readings, or by performing resistance tests on the sensor and comparing the values to the manufacturer's specifications.
Common wiring issues include damaged or chafed wires, loose connectors, corrosion, shorts to ground or voltage, and improper wire routing or securement.
To locate a short circuit to voltage, you need to carefully inspect the entire wiring harness for any signs of chafing, pinching, or damage, and check for potential short points near power sources or other electrical components.
While it is possible to replace the pressure sensor yourself, it is recommended to follow the manufacturer's recommended procedure carefully and use only OEM or high-quality aftermarket sensors to ensure proper installation and longevity.
The pressure sensor should be replaced according to the manufacturer's recommended maintenance schedule, typically based on mileage or time intervals. Inspecting the sensor during routine maintenance can also help identify the need for replacement.
If the P03A2 code is not repaired, it can lead to further damage to the engine, decreased fuel efficiency, and potential drivability issues. Ignoring the code can also cause additional codes to be set, complicating the diagnosis and repair process.
While aftermarket wiring harnesses or connectors may be more cost-effective, it is recommended to use OEM or high-quality aftermarket parts to ensure compatibility, proper fit, and longevity. Low-quality parts may fail prematurely and cause additional issues.
To prevent future wiring issues, ensure proper wire routing and protection from heat sources, debris, and potential chafe points. Use appropriate wire loom or conduit for protection, and secure wires properly to prevent excessive movement or strain.
If the P03A2 code persists after repairs, it is recommended to double-check the diagnostic process, verify the repair work, and consider seeking professional assistance from a qualified mechanic or dealership to identify any remaining issues.
Miguel started tinkering with car radios as a teenager, fascinated by the intricate dance of wires and circuits. This passion led him to pursue a career as an automotive electrician. For the past 10 years, Miguel has tackled everything from flickering headlights to mysterious electrical gremlins. He thrives on troubleshooting electrical problems and enjoys sharing his knowledge to empower car owners to understand their vehicles better.