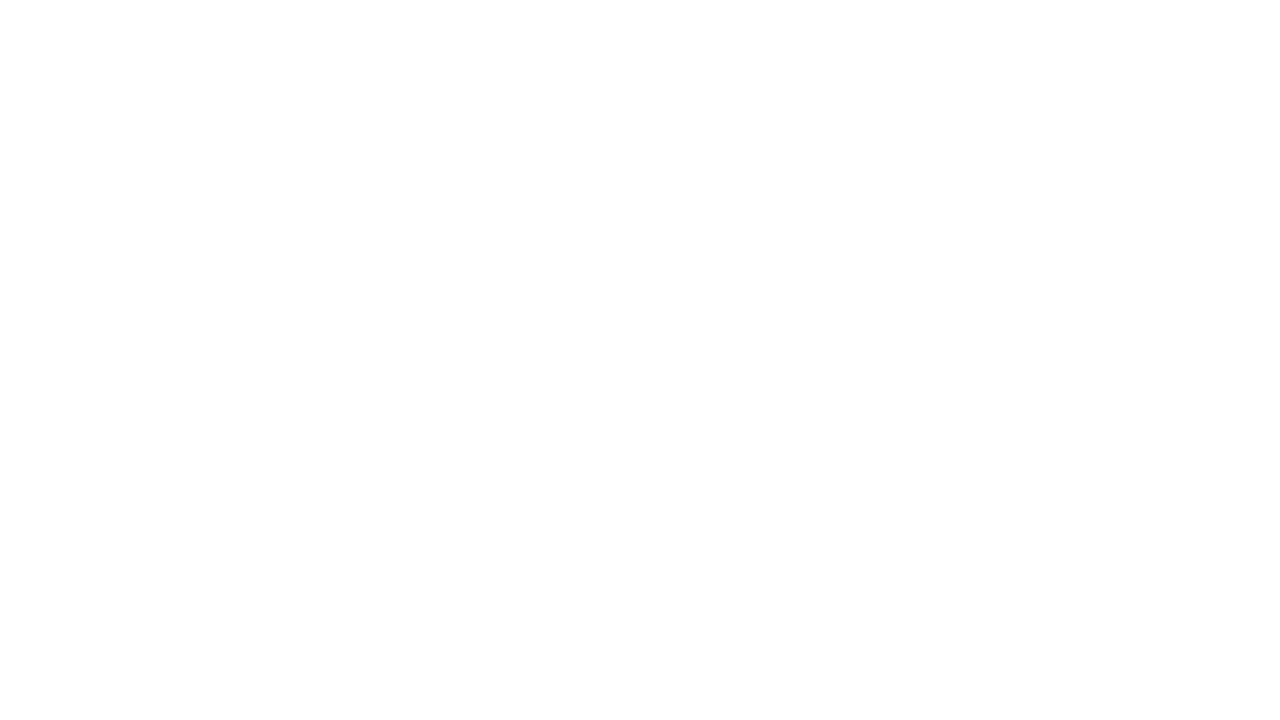
The LS engine family from General Motors has been widely used in various vehicles, from performance cars to trucks, since its introduction in the late 1990s. One crucial aspect of proper LS engine assembly and maintenance is the correct torquing procedure for the rocker arms. Rocker arms are responsible for transferring the motion from the camshaft to the valves, and their proper installation and torque are essential for optimal engine performance and longevity.
One of the most common issues I've encountered is the dreaded rocker arm needle bearing walk-out. Imagine this scenario: you're cruising down the highway, revving that LS engine to its limits, when suddenly, those tiny needle bearings decide to take a stroll – right into the depths of your engine. It's a nightmare, I tell you!
Issue | Description |
---|---|
Needle Bearing Walk-Out | Rocker arm needle bearings walking out of the trunnion, causing bearing needles to scatter inside the engine. More likely at high RPMs and with high valve spring pressures. |
Rocker Arm Rotation | Rocker arms rotating slightly when torqued down, causing the rocker tip to misalign with the valve stem tip. Can happen if the lifter is not on the base circle of the cam lobe when torquing the rocker. |
Another common problem is the rocker arm rotation during torquing. It might seem like a minor hiccup, but trust me, it can lead to misalignment between the rocker tip and the valve stem tip. And when that happens, you'll hear a telltale ticking or tapping noise from the valve train, which only gets faster (but not louder) as the RPMs increase. It's like a ticking time bomb, waiting to wreak havoc on your engine.
So, how do you catch these issues before they spiral out of control? Well, my friends, it all starts with regular inspections and a keen ear.
Check for loose needle bearings in the oil or stuck to the oil drain plug during oil changes.
Listen for a ticking/tapping noise from the valve train, which may get faster with increasing RPM but not louder.
Remove rocker arms and use a straightedge to check if all valve stems are at the same height, indicating a bent valve if one is lower.
If you hear that dreaded ticking or tapping noise, it's time to roll up your sleeves and get to work. Remove those rocker arms and grab a trusty straightedge. Check if all the valve stems are at the same height – if one's lower than the rest, you might have a bent valve on your hands. Trust me, you don't want to ignore that warning sign.
Now, let's talk about fixing these issues and preventing them from happening again. First things first, invest in a quality rocker arm trunnion and bearing upgrade kit, like the Comp Cams 13702-KIT. These kits come with caged roller bearings and circlips, which act as a safety net, preventing those pesky needle bearings from taking an unplanned vacation.
Repair Step | Description |
---|---|
Upgrade Kit | Replace rocker arm trunnions and bearings with an upgraded kit like Comp Cams 13702-KIT with caged roller bearings and circlips to prevent bearing walk-out. |
Lifter Position | When reinstalling rockers, rotate the crankshaft to position each cylinder's lifter on the base circle of the cam before torquing that cylinder's rockers. |
Torque Sequence | Torque rocker bolts in the proper sequence and to the specified 22 ft-lbs torque. |
When reinstalling the rocker arms, pay close attention to the crankshaft position. Rotate it until each cylinder's lifter is on the base circle of the cam before torquing that cylinder's rockers. It's a crucial step that can save you a world of trouble down the line.
And let's not forget about proper torque specifications. Those rocker bolts need to be torqued in the correct sequence and to the specified 22 ft-lbs of torque. It might seem like a small detail, but trust me, it can make all the difference in the world.
As the saying goes, "an ounce of prevention is worth a pound of cure." In the case of LS rocker arm torque, this couldn't be more true.
Upgrade to better rocker arm trunnions and bearings, especially for high-performance applications.
Follow the proper torquing procedure, ensuring lifters are on the base circle when torquing each rocker.
Periodic inspection and maintenance as recommended by the manufacturer.
Upgrading to better rocker arm trunnions and bearings, especially for high-performance applications, is a wise investment. It's like giving your engine a suit of armor against those pesky bearing walk-outs.
But prevention doesn't stop there. Follow the proper torquing procedure to a tee, ensuring those lifters are on the base circle when torquing each rocker. It might seem tedious, but it's a small price to pay for peace of mind and a smooth-running engine.
And let's not forget about regular maintenance. Periodic inspections and following the manufacturer's recommended service intervals can go a long way in catching potential issues before they escalate.
Now, let's address the elephant in the room – the cost.
Cost Item | Approximate Cost |
---|---|
Comp Cams LS Rocker Trunnion Upgrade Kit 13702-KIT | $100 - $150 |
Labor Costs for R&R and Upgrade | Varies |
Potential Engine Damage Costs | Potentially Expensive |
Upgrading to a kit like the Comp Cams 13702-KIT will set you back around $100 to $150, but trust me, it's a small price to pay for the peace of mind it provides. And let's not forget about labor costs if you're not the DIY type. Having a professional handle the rocker arm removal, replacement, and torquing can save you a lot of headaches in the long run.
But here's the kicker: the potential costs of engine damage if those bearing needles start circulating before you address the issue can be astronomical. We're talking about expensive repairs, potential engine replacements, and a whole lot of heartache. So, in the grand scheme of things, investing in proper maintenance and upgrades is a no-brainer.
Fellow gearheads, I hope this deep dive into the world of LS rocker arm torque has been both informative and entertaining. Remember, paying attention to these seemingly small details can mean the difference between a smooth-running engine and a costly repair nightmare. Embrace the knowledge, follow the proper procedures, and never underestimate the importance of rocker arm torque. Your LS engine will thank you for it, and you'll be able to enjoy many more miles of high-performance driving bliss.
So, keep those wrenches spinning, and never stop learning. The world of automotive mechanics is a fascinating one, and there's always something new to discover. Until next time, happy wrenching!
Needle bearing walk-out is more likely to occur at high RPMs and with high valve spring pressures. It happens when the needle bearings in the rocker arm trunnion escape and scatter inside the engine.
Check for loose needle bearings in the oil or stuck to the drain plug during oil changes. Listen for a ticking/tapping noise from the valve train that gets faster with increasing RPM.
The rocker arm bolts should be torqued in the proper sequence to 22 ft-lbs of torque.
Positioning each cylinder's lifter on the base circle of the cam before torquing that cylinder's rockers prevents rocker arm rotation and misalignment.
The Comp Cams 13702-KIT rocker arm trunnion and bearing upgrade kit with caged roller bearings and circlips prevents needle bearing walk-out.
Remove the rocker arms and use a straightedge to check if all valve stems are at the same height. A lower valve stem indicates a bent valve.
Regular inspections and following the manufacturer's service intervals can catch potential rocker arm issues before they escalate into major problems.
Ignoring rocker arm issues can lead to expensive engine damage costs, potentially requiring a full engine replacement.
While not absolutely necessary for stock engines, upgraded rocker arm components provide added insurance and peace of mind, especially for high-performance applications.
Upgrading rocker arm components requires removal and reinstallation, which can be a complex job for those without mechanical experience. Professional installation may be advisable.
Sarah isn't your average gearhead. With a double major in Mechanical Engineering and Automotive Technology, she dived straight into the world of car repair. After 15 years of turning wrenches at dealerships and independent shops, Sarah joined MICDOT to share her expertise and passion for making cars run like new. Her in-depth knowledge and knack for explaining complex issues in simple terms make her a valuable asset to our team.