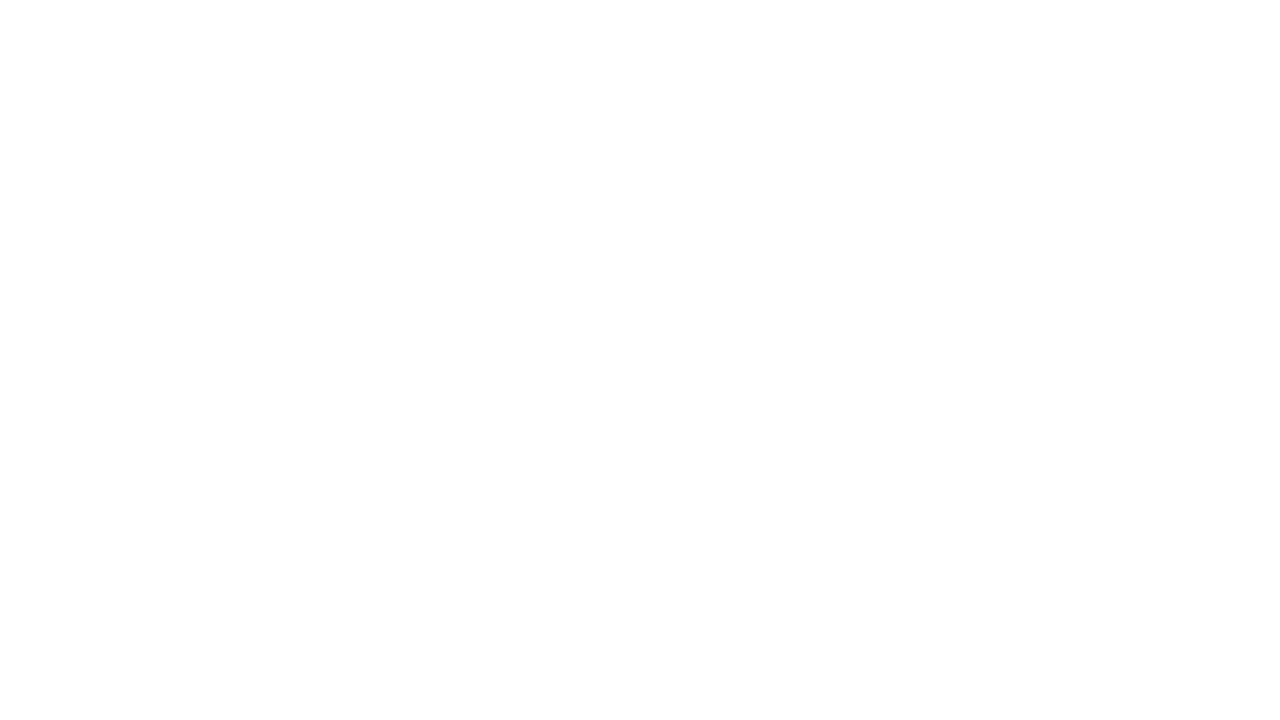
In the relentless pursuit of enhanced vehicle performance, fuel efficiency, and reduced environmental impact, the automotive industry has turned its attention to innovative materials that can revolutionize traditional components. Among these cutting-edge solutions, titanium alloys have emerged as a game-changer for car exhaust systems, offering a unique combination of properties that address the demanding requirements of this critical component.
The automotive industry's constant drive for improved vehicle performance and fuel efficiency has fueled the search for lightweight and high-performance materials. Reducing vehicle weight is a crucial factor in achieving these goals, as it directly contributes to better acceleration, handling, and fuel economy. Traditional materials used in exhaust systems, such as stainless steel, have limitations in terms of weight and high-temperature resistance. To overcome these challenges, automakers have turned to advanced materials that can deliver superior performance while reducing overall vehicle mass.
Titanium alloys have emerged as a game-changer in this quest, offering a unique blend of properties that make them well-suited for automotive exhaust applications. Their low density, high strength-to-weight ratio, superior corrosion resistance, and exceptional high-temperature capabilities have positioned them as a revolutionary solution for car exhaust systems.
Titanium alloys possess several remarkable characteristics that set them apart from traditional materials, making them ideal candidates for exhaust system applications. The following table summarizes the key properties of titanium alloys and their advantages in exhaust system applications:
Property | Advantage |
---|---|
Low density | Significant weight savings, contributing to improved fuel efficiency and acceleration performance |
High strength-to-weight ratio | Exceptional strength, ensuring durability and structural integrity even under extreme operating conditions |
Superior corrosion resistance | Protection against corrosive exhaust gases and road salts, extending the lifespan of exhaust systems |
High-temperature resistance | Ability to withstand extreme exhaust gas temperatures without significant degradation, maintaining consistent performance |
One of the most significant advantages of titanium alloys is their low density, approximately 60% that of steel. This property translates into substantial weight savings when used in exhaust system components, directly contributing to improved fuel efficiency and acceleration performance. By reducing the overall vehicle weight, titanium alloy exhaust systems can significantly impact fuel consumption and vehicle dynamics.
Despite their lightweight nature, titanium alloys exhibit exceptional strength-to-weight ratios. Some alloys can reach tensile strengths over 800 MPa, ensuring the durability and structural integrity of exhaust components even under extreme operating conditions. This high strength allows for the design of lightweight yet robust exhaust systems that can withstand the rigors of high-performance driving and harsh environments.
Titanium alloys demonstrate superior corrosion resistance, protecting against the corrosive effects of exhaust gases and road salts. This characteristic extends the lifespan of exhaust systems, reducing maintenance costs and downtime associated with premature component failure. The corrosion-resistant properties of titanium alloys ensure that exhaust components maintain their structural integrity and performance over an extended period, minimizing the need for frequent replacements.
A critical advantage of titanium alloys in exhaust applications is their high-temperature resistance. As exhaust gas temperatures can exceed 700°C, the ability to withstand such extreme conditions without significant degradation is essential for maintaining consistent performance and longevity. Titanium alloys can withstand these high temperatures without compromising their mechanical properties or undergoing significant oxidation, ensuring reliable operation and extended service life.
The unique properties of titanium alloys translate into several tangible benefits when employed in automotive exhaust systems, revolutionizing vehicle performance, efficiency, and environmental impact.
By replacing traditional materials like stainless steel with lightweight titanium alloys, automakers can achieve significant weight savings in exhaust system components. For example, a titanium exhaust system for the Volkswagen Golf 4motion resulted in a 50% weight reduction compared to its steel counterpart. This reduction in overall vehicle weight directly contributes to better fuel economy, as studies have shown that for every 10% decrease in vehicle weight, fuel consumption can decrease by 6-8%.
Lightweight titanium exhaust components not only improve fuel efficiency but also enhance overall vehicle performance. The reduced mass of the exhaust system leads to improved acceleration, handling, and braking capabilities, providing a more dynamic and responsive driving experience. By reducing the overall vehicle weight, titanium alloy exhaust systems contribute to better power-to-weight ratios, resulting in improved acceleration and agility.
The exceptional corrosion resistance and high-temperature capabilities of titanium alloys extend the lifespan of exhaust systems, minimizing the need for frequent replacements. This durability not only reduces maintenance costs but also contributes to a more sustainable approach by reducing waste and promoting a circular economy. With their superior resistance to corrosion and high temperatures, titanium alloy exhaust components can withstand harsh operating conditions for an extended period, ensuring reliable performance and minimizing downtime.
The smooth internal surfaces of titanium exhaust pipes and mufflers facilitate better exhaust flow, reducing backpressure and improving engine efficiency. This results in optimized engine performance and potentially better fuel economy. By minimizing restrictions in the exhaust system, titanium alloy components allow for more efficient exhaust gas flow, reducing backpressure and enabling the engine to operate at peak efficiency.
In addition to their functional benefits, titanium exhaust systems also offer a distinctive aesthetic appeal. The unique luster and color of titanium add a premium and sporty appearance to high-performance vehicles, enhancing their visual appeal and desirability. The sleek and modern look of titanium exhaust components can complement the design of high-end sports cars and performance vehicles, contributing to their overall aesthetic appeal.
While commercially pure (CP) titanium has been used in exhaust applications, its limited high-temperature strength and oxidation resistance have prompted the development of specialized titanium alloys tailored for the demanding requirements of exhaust systems.
Although CP titanium offers advantages in terms of weight and corrosion resistance, its high-temperature strength and oxidation resistance are limited, restricting its use in certain exhaust system components. To overcome these limitations, various titanium alloy compositions have been developed, each offering unique properties and advantages for exhaust system applications.
The following table provides an overview of some commonly used titanium alloys for exhaust system applications, along with their key properties and advantages:
Alloy | Properties and Advantages |
---|---|
Ti-6Al-4V | Widely employed in automotive applications, including exhaust valves and manifolds, due to its excellent strength and oxidation resistance up to 600°C. |
TIMETAL® Exhaust XT | A patented low-alloy titanium developed specifically for exhaust systems, offering improved high-temperature strength and oxidation resistance compared to CP titanium. |
Ti-1.2ASN | Developed by Kobe Steel, this alloy exhibits enhanced formability and high-temperature strength, making it suitable for exhaust components subjected to complex forming operations. |
Ti-1Cu-0.5Nb | Introduced by Nippon Steel, this alloy features solid solution hardening and low oxygen content, resulting in doubled high-temperature strength compared to CP titanium. |
Super-TIX® 10CU | A specially developed titanium alloy for high-performance motorsport exhaust systems, offering a combination of high-temperature strength and good formability at room temperature. |
These specialized alloy compositions are designed to address the specific requirements of exhaust system components, such as high-temperature strength, oxidation resistance, formability, and corrosion resistance. By tailoring the alloy composition, manufacturers can optimize the properties of titanium exhaust components to meet the demanding operating conditions and performance requirements of modern vehicles.
Titanium alloys find applications in various components of automotive exhaust systems, each playing a crucial role in optimizing performance, efficiency, and durability. The following table outlines the common applications of titanium alloys in exhaust system components:
Component | Application |
---|---|
Exhaust Pipes and Tubing | Titanium alloy pipes and tubing offer weight savings, corrosion resistance, and improved exhaust flow compared to traditional materials. |
Mufflers and Silencers | Titanium mufflers and silencers not only reduce weight but also maintain their structural integrity at high temperatures, ensuring consistent performance and noise reduction. |
Catalytic Converters | The high-temperature resistance and corrosion-resistant properties of titanium alloys make them suitable for catalytic converter housings and substrates, contributing to reduced emissions. |
Exhaust Manifolds and Headers | Titanium alloy manifolds and headers can withstand the extreme temperatures and pressures generated by high-performance engines, while contributing to weight reduction and improved exhaust gas flow. |
By leveraging the unique properties of titanium alloys in these critical exhaust system components, automakers can achieve significant improvements in performance, efficiency, and durability while meeting stringent emission regulations and environmental standards.
The production of titanium exhaust systems involves various manufacturing processes, each presenting unique challenges that must be addressed to ensure optimal performance and quality.
Forming operations, such as bending, stretching, and drawing, are essential for shaping titanium alloy components into the desired geometries. However, these processes require careful consideration of the alloy's ductility and formability characteristics to prevent defects and ensure dimensional accuracy.
Bending, Stretching, and Drawing: Techniques like bending, stretching, and drawing are employed to form titanium alloy exhaust components into their final shapes. These processes must be carefully controlled to account for the material's unique properties and prevent cracking or deformation.
Alloy Ductility and Formability: Different titanium alloys exhibit varying degrees of ductility and formability, which influence their behavior during forming operations. Alloys like Ti-1.2ASN are specifically designed to enhance formability, enabling the production of complex exhaust system geometries.
Joining titanium alloy components requires specialized welding techniques and equipment to ensure strong, defect-free joints capable of withstanding the harsh operating conditions of exhaust systems. The following welding methods are commonly employed:
Gas Tungsten Arc Welding (GTAW): Also known as TIG welding, this process offers precise control and produces high-quality welds with minimal distortion, making it suitable for joining titanium alloy exhaust components.
Laser Beam Welding (LBW): This advanced welding technique utilizes a highly focused laser beam to fuse the materials, resulting in narrow and deep welds with minimal heat-affected zones, which is advantageous for welding titanium alloys.
To enhance the appearance, corrosion resistance, or mechanical properties of titanium exhaust components, surface finishing and heat treatment processes may be employed. These techniques can include:
Polishing: Polishing can improve the aesthetic appeal of titanium exhaust components by enhancing their luster and creating a smooth, reflective surface.
Anodizing: Anodizing is a surface treatment process that creates a protective oxide layer on the titanium surface, improving corrosion resistance and providing a range of color options.
Heat Treatment: Specialized heat treatments can be applied to titanium alloy exhaust components to modify their mechanical properties, such as strength, ductility, or hardness, depending on the specific application requirements.
By carefully controlling these manufacturing processes, manufacturers can ensure that titanium exhaust systems meet the highest standards of quality, performance, and durability.
Titanium exhaust systems have found widespread adoption in high-performance vehicles, racing cars, and motorcycles, where weight savings and durability are paramount. Notable examples include:
Nissan GT-R: The Nissan GT-R sports car features a titanium exhaust system made from Super-TIX® 10CU, resulting in a 5.5 kg weight reduction compared to the original stainless steel version. This weight savings contributes to improved acceleration and handling performance.
Akrapovic: Akrapovic, a leading manufacturer of high-performance exhaust systems, extensively utilizes titanium alloys such as Exhaust XT, Ti-1.2ASN, and Ti-1Cu-0.5Nb in their products for motorcycles and sports cars, leveraging the lightweight and high-temperature capabilities of these alloys.
Porsche: Porsche has embraced the use of titanium exhaust systems in their high-performance models, taking advantage of the material's lightweight and high-temperature capabilities to enhance vehicle dynamics and performance.
These successful applications demonstrate the real-world benefits of titanium alloy exhaust systems and their ability to deliver exceptional performance, efficiency, and durability in demanding automotive environments.
While the benefits of titanium exhaust systems are compelling, their widespread adoption in mainstream vehicles has been hindered by cost considerations. The raw material costs and specialized manufacturing processes associated with titanium alloys contribute to higher overall system costs compared to traditional materials like stainless steel.
However, as demand for lightweight and high-performance vehicles continues to grow, and manufacturing processes become more efficient, the cost gap is expected to narrow. Additionally, the potential for long-term cost savings through reduced fuel consumption and extended component lifespan may offset the initial higher investment.
Furthermore, ongoing research and development efforts are focused on refining titanium alloy compositions and processing techniques to further enhance their properties and reduce manufacturing costs, paving the way for broader adoption in the automotive industry.
Beyond performance and durability advantages, the use of lightweight titanium exhaust systems contributes to environmental sustainability. By reducing vehicle weight and improving fuel efficiency, titanium exhaust systems indirectly lower greenhouse gas emissions and the overall carbon footprint of vehicles.
Moreover, the corrosion resistance and extended lifespan of titanium exhaust components reduce the need for frequent replacements, minimizing waste and promoting a circular economy approach.
While titanium alloys offer numerous advantages over traditional materials like stainless steel, it is essential to acknowledge potential drawbacks or limitations:
Consideration | Titanium Alloys | Stainless Steel |
---|---|---|
Cost | Higher raw material costs and specialized manufacturing processes can result in higher overall system costs. | Lower material and manufacturing costs. |
Oxidation Resistance | Excellent oxidation resistance at high temperatures, but some alloys may experience oxidation and embrittlement above certain temperature thresholds. | Good oxidation resistance at high temperatures. |
Formability | Newer titanium alloys have improved formability, but some alloys may still require specialized forming techniques and equipment. | Generally good formability. |
Welding Challenges | Welding titanium alloys can be more challenging, requiring specialized equipment and techniques to ensure strong, defect-free joints. | Relatively easier to weld compared to titanium alloys. |
Despite these potential limitations, the advantages of titanium alloys in terms of weight savings, strength, corrosion resistance, and high-temperature performance often outweigh the drawbacks, particularly in high-performance and racing applications.
The integration of titanium alloys into automotive exhaust systems represents a significant step forward in the pursuit of enhanced vehicle performance, fuel efficiency, and environmental sustainability. With their unique combination of lightweight, high strength, corrosion resistance, and high-temperature capabilities, titanium alloys offer a compelling solution to the demanding requirements of modern exhaust systems.
From high-performance sports cars and racing vehicles to mainstream passenger cars, the adoption of titanium exhaust systems has the potential to revolutionize the automotive industry. As research and development efforts continue to refine alloy compositions and manufacturing processes, the cost barriers are expected to diminish, paving the way for broader adoption and unlocking the full potential of these remarkable materials.
By embracing the advantages of titanium alloys in exhaust system design, automakers can deliver vehicles that not only excel in performance but also contribute to a more sustainable and environmentally conscious future for the automotive industry.
##FAQs
Titanium alloys offer low density for weight reduction and high strength-to-weight ratio. They also provide superior corrosion resistance and high-temperature capabilities compared to traditional materials.
Lightweight titanium exhaust components reduce the overall vehicle weight, leading to better fuel economy. Studies show that a 10% decrease in vehicle weight can decrease fuel consumption by 6-8%.
Alloys like TIMETAL® Exhaust XT, Ti-1.2ASN, Ti-1Cu-0.5Nb, and Super-TIX® 10CU are developed specifically for improved high-temperature strength, oxidation resistance, and formability in exhaust applications.
The reduced mass of titanium exhaust components leads to improved acceleration, handling, and braking capabilities, providing a more dynamic and responsive driving experience.
Lightweight titanium exhaust systems contribute to reduced greenhouse gas emissions and lower carbon footprint by improving fuel efficiency. Their extended lifespan also minimizes waste and promotes a circular economy.
Forming operations and welding techniques require careful consideration due to the unique properties of titanium alloys. Surface finishing and heat treatments may also be employed to enhance appearance and mechanical properties.
Titanium exhaust systems are generally more expensive than traditional materials like stainless steel due to higher raw material costs and specialized manufacturing processes.
Notable examples include the Nissan GT-R, Porsche high-performance models, and exhaust systems from manufacturers like Akrapovic, which leverage the lightweight and high-temperature capabilities of titanium alloys.
The extended lifespan and corrosion resistance of titanium exhaust components reduce the need for frequent replacements, minimizing waste and promoting a circular economy approach.
Potential limitations include higher costs, challenges in formability and welding, and potential oxidation or embrittlement at extremely high temperatures for some alloys.
Sarah isn't your average gearhead. With a double major in Mechanical Engineering and Automotive Technology, she dived straight into the world of car repair. After 15 years of turning wrenches at dealerships and independent shops, Sarah joined MICDOT to share her expertise and passion for making cars run like new. Her in-depth knowledge and knack for explaining complex issues in simple terms make her a valuable asset to our team.