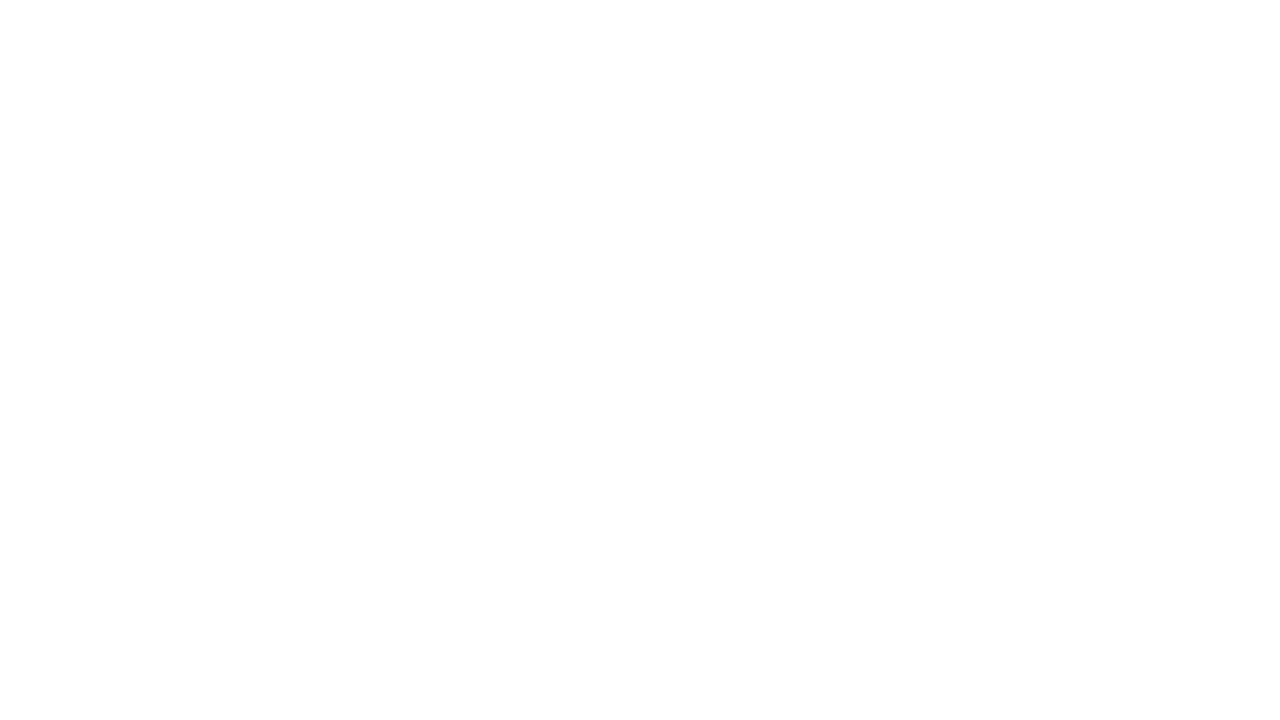
Brake boosting systems are essential components in modern vehicles that enhance safety by amplifying the force applied to the brakes during emergency situations. These systems ensure that drivers can stop their vehicles quickly and effectively, even when faced with unexpected hazards on the road. In this article, we will explore the various aspects of brake boosting systems, including their types, how they work, their benefits, and their importance in ensuring vehicle safety.
Brake boosting is a technology that has revolutionized the automotive industry by significantly improving vehicle safety. It works by amplifying the force applied to the brakes when the driver presses the brake pedal, especially during emergency braking situations. This article will delve into the different types of brake boosting systems, their activation, benefits, integration with other safety features, maintenance, and factors affecting their performance. We will also discuss the history and development of brake boosting, its prevalence in modern vehicles, and its effectiveness in reducing stopping distances.
There are three main types of brake boosting systems used in vehicles today: hydraulic, pneumatic, and electro-hydraulic. Each type has its unique characteristics and advantages.
Hydraulic brake boosting systems use fluid pressure to amplify the force applied to the brakes. When the driver presses the brake pedal, a piston in the master cylinder pressurizes the brake fluid, which is then transmitted to the brake calipers or wheel cylinders. The hydraulic booster multiplies this force, allowing for greater stopping power with less pedal effort.
Pneumatic brake boosting systems, also known as vacuum-assisted brakes, use a vacuum generated by the engine to amplify the force applied to the brakes. When the driver presses the brake pedal, a valve opens, allowing air to flow into a diaphragm chamber. The difference in pressure between the vacuum and the atmospheric pressure creates a force that assists in applying the brakes.
Electro-hydraulic brake boosting systems combine the benefits of hydraulic and electric systems. In this type of system, an electric motor drives a pump that pressurizes the brake fluid. When the driver presses the brake pedal, sensors detect the force applied and send a signal to the electric motor, which then generates the appropriate amount of hydraulic pressure to assist in braking.
Type | Mechanism | Advantages |
---|---|---|
Hydraulic | Fluid pressure amplifies force | Simple, reliable, widely used |
Pneumatic | Vacuum generated by engine amplifies force | Cost-effective, easy to maintain |
Electro-hydraulic | Electric motor drives hydraulic pump | Precise control, integration with electronic safety features |
Brake boosting systems work by amplifying the force applied to the brakes and reducing the stopping distance of the vehicle.
When the driver presses the brake pedal, the brake boosting system multiplies the force applied, making it easier for the driver to generate the necessary stopping power. This amplification is achieved through the use of hydraulic, pneumatic, or electro-hydraulic systems, depending on the type of brake booster installed in the vehicle.
By amplifying the force applied to the brakes, brake boosting systems help reduce the stopping distance of the vehicle. This is particularly important in emergency braking situations, where every fraction of a second counts. With a brake booster, the vehicle can come to a stop more quickly, potentially avoiding accidents or minimizing their severity.
Brake boosting systems are designed to activate in specific situations to provide the necessary assistance to the driver.
In emergency braking situations, such as when a driver needs to stop suddenly to avoid a collision, brake boosting systems automatically activate to provide maximum braking force. This helps the driver bring the vehicle to a stop as quickly as possible, minimizing the risk of an accident.
Panic stops occur when a driver suddenly and forcefully applies the brakes, often in response to an unexpected hazard. In these situations, the brake booster quickly activates to provide the necessary force amplification, ensuring that the vehicle stops in the shortest possible distance.
Brake boosting systems offer several key benefits that contribute to overall vehicle safety and driver confidence.
The primary benefit of brake boosting is improved vehicle safety. By reducing stopping distances and providing greater braking force, these systems help drivers avoid accidents or minimize their severity. This is especially important in emergency situations where quick and effective braking can make the difference between a close call and a serious collision.
Brake boosting systems also enhance vehicle control by providing a more consistent and predictable braking response. With the assistance of a brake booster, drivers can apply the brakes smoothly and progressively, maintaining better control over the vehicle during deceleration. This is particularly beneficial in challenging driving conditions, such as wet or slippery roads.
Brake boosting systems are often integrated with other advanced safety features to provide comprehensive protection for drivers and passengers.
Anti-lock Braking Systems (ABS) work in conjunction with brake boosters to prevent wheel lockup during heavy braking. When the ABS sensors detect that one or more wheels are about to lock up, the system rapidly modulates the brake pressure, allowing the wheels to continue rotating. This helps maintain steering control and stability, even during emergency braking situations.
Electronic Stability Control (ESC) is another advanced safety feature that works with brake boosting systems to enhance vehicle stability and control. ESC continuously monitors the vehicle's direction and compares it to the driver's intended path. If the system detects a discrepancy, it can selectively apply the brakes on individual wheels and adjust engine power to help the driver maintain control and prevent skidding or spinning.
Safety Feature | Function | Integration with Brake Boosting |
---|---|---|
ABS | Prevents wheel lockup during heavy braking | Brake booster provides necessary force for rapid brake modulation |
ESC | Enhances vehicle stability and control | Brake booster enables precise, selective braking on individual wheels |
EBD | Optimizes brake force distribution between front and rear | Brake booster amplifies force for optimal distribution |
BAS | Applies maximum braking force in emergency situations | Brake booster enhances force applied by BAS |
To ensure that brake boosting systems continue to function effectively, regular maintenance is essential.
One of the most important maintenance tasks for brake boosting systems is regular brake fluid changes. Over time, brake fluid can absorb moisture and become contaminated, reducing its effectiveness and potentially causing damage to the braking system. By changing the brake fluid at the recommended intervals, drivers can maintain the performance and reliability of their brake boosters.
Another crucial aspect of brake booster maintenance is checking for leaks. A leak in the brake boosting system can result in a loss of pressure and reduced braking performance. Regular inspections of the brake lines, hoses, and connections can help identify and address any leaks before they become a serious problem.
Several external factors can impact the performance of brake boosting systems, and drivers should be aware of these to ensure optimal braking performance.
At higher altitudes, the air pressure is lower, which can affect the performance of pneumatic brake boosting systems. In these conditions, the vacuum generated by the engine may be less effective, resulting in reduced braking assistance. Some vehicles are equipped with altitude compensation devices to mitigate this effect.
Extreme temperatures can also impact brake boosting performance. In very cold weather, the brake fluid may become thicker, reducing its ability to flow freely through the system. This can result in a spongy or unresponsive brake pedal. Conversely, in very hot conditions, the brake fluid may become too thin, leading to a loss of braking power. Regular brake fluid changes and maintaining the proper fluid level can help minimize these temperature-related issues.
While most modern vehicles come equipped with brake boosting systems, older vehicles may not have this technology. However, it is possible to retrofit brake boosters to many older vehicles, providing them with the benefits of enhanced braking performance and safety. Retrofitting a brake booster typically involves installing a new master cylinder, brake booster, and associated hardware. It is important to ensure that the retrofit kit is compatible with the vehicle's make and model and that the installation is performed by a qualified mechanic.
Brake boosting technology has a long and fascinating history, dating back to the early days of the automotive industry. The first brake boosters were introduced in the 1920s and used a vacuum-assisted system to reduce the effort required to apply the brakes. Over time, brake boosting systems have evolved to incorporate hydraulic and electro-hydraulic technologies, providing even greater levels of performance and reliability. Today, brake boosters are an essential component of modern vehicle safety systems, and their continued development promises to bring even more advanced features and capabilities in the future.
Brake boosting systems are now standard equipment on the vast majority of modern vehicles. From compact cars to large trucks and SUVs, nearly every new vehicle sold today comes equipped with some form of brake booster. This widespread adoption of brake boosting technology is a testament to its effectiveness in enhancing vehicle safety and driver confidence. As automotive technology continues to advance, it is likely that brake boosting systems will become even more sophisticated and integrated with other safety features, providing drivers with an ever-increasing level of protection on the road.
The effectiveness of brake boosting systems in reducing stopping distances has been well-established through numerous studies and real-world experience. By amplifying the force applied to the brakes, brake boosters can help vehicles come to a stop up to 20% faster than vehicles without this technology. This reduction in stopping distance can mean the difference between a close call and a serious accident, particularly in emergency braking situations. The table below illustrates the potential reduction in stopping distance provided by brake boosting systems:
Vehicle Speed (mph) | Stopping Distance without Brake Booster (ft) | Stopping Distance with Brake Booster (ft) |
---|---|---|
30 | 75 | 60 |
60 | 240 | 192 |
90 | 480 | 384 |
As the table shows, the benefits of brake boosting become even more pronounced at higher speeds, where the reduction in stopping distance can be significant.
While brake boosting systems provide significant benefits on their own, they are particularly important for vehicles equipped with Anti-lock Braking Systems (ABS) and Electronic Stability Control (ESC). These advanced safety features rely on the rapid and precise application of braking force to individual wheels, which is made possible by the force amplification provided by brake boosters. Without a brake booster, the effectiveness of ABS and ESC would be greatly diminished, as the systems would not be able to apply the necessary braking force quickly enough to maintain vehicle control and stability.
Brake boosting technology has come a long way since its introduction in the early 20th century. Today, brake boosters are more advanced, reliable, and effective than ever before. Some of the latest developments in brake boosting technology include:
Electronic brake force distribution (EBD): This system optimizes the distribution of braking force between the front and rear wheels based on factors such as vehicle load and weight distribution.
Brake assist systems (BAS): These systems use sensors to detect when the driver is attempting an emergency stop and automatically apply maximum braking force to help reduce stopping distances.
Regenerative braking: In hybrid and electric vehicles, regenerative braking systems use the vehicle's electric motor to slow the vehicle down, converting kinetic energy into electrical energy that can be stored in the battery for later use.
As automotive technology continues to evolve, it is likely that brake boosting systems will become even more advanced, integrating with other safety features and adapting to changing driving conditions in real-time.
Brake boosting systems play a crucial role in ensuring safe driving, particularly in emergency situations where quick and effective braking can make all the difference. By amplifying the force applied to the brakes and reducing stopping distances, brake boosters help drivers maintain control of their vehicles and avoid accidents. This is especially important in today's driving environment, where distractions and hazards are more prevalent than ever before. By investing in vehicles equipped with advanced brake boosting systems and maintaining these systems properly, drivers can significantly enhance their safety on the road and reduce the risk of serious accidents.
While brake boosting systems offer numerous benefits, there are also some potential drawbacks to consider.
One potential drawback of brake boosting systems is their increased complexity compared to traditional braking systems. With the addition of hydraulic, pneumatic, or electro-hydraulic components, brake boosters introduce more potential points of failure and require more specialized knowledge to diagnose and repair. This can lead to higher maintenance costs and potentially longer repair times in the event of a problem.
Another potential issue with brake boosting systems is their impact on brake pedal feel. Some drivers may find that the assisted braking provided by a brake booster results in a less direct or responsive pedal feel, which can take some getting used to. This is particularly true for drivers who are accustomed to the more direct feel of non-assisted brakes. However, most drivers quickly adapt to the feel of assisted brakes and appreciate the reduced effort required to apply the brakes.
While brake boosting systems are designed to enhance safety and make driving easier, some drivers may require a period of adaptation when first using these systems. This is particularly true for drivers who are accustomed to non-assisted brakes, as the feel and response of assisted brakes can be quite different. Some tips for adapting to brake boosting systems include:
Practice in a safe environment: When first using a vehicle with brake boosting, it is a good idea to practice braking in a safe, controlled environment, such as an empty parking lot, to get a feel for the system's response.
Adjust your braking technique: With brake boosting, less pedal effort is required to achieve the same level of braking force. As a result, drivers may need to adjust their braking technique to avoid over-braking or making abrupt stops.
Trust the system: Brake boosting systems are designed to provide optimal braking performance in a wide range of situations. Drivers should trust the system to do its job and resist the urge to pump the brakes or apply excessive force, which can actually reduce the effectiveness of the brake booster.
By taking the time to adapt to brake boosting systems and understanding how they function, drivers can fully realize the benefits of this technology and enhance their overall safety on the road.
The widespread adoption of brake boosting systems in modern vehicles is based on several key assumptions and premises:
Drivers want and need assistance in braking: One of the main assumptions behind brake boosting is that drivers benefit from assistance in applying the brakes, particularly in emergency situations where quick and decisive action is required.
Assisted braking enhances safety: Another key premise is that brake boosting systems enhance overall vehicle safety by reducing stopping distances and providing drivers with greater control over their vehicles.
The benefits outweigh the costs: While brake boosting systems add complexity and cost to vehicle braking systems, the assumption is that the safety benefits they provide more than justify these additional expenses.
Drivers will adapt to assisted braking: Finally, there is an assumption that drivers will be able to quickly adapt to the feel and performance of brake boosting systems, and that any initial learning curve will be outweighed by the long-term benefits of the technology.
While these assumptions and premises have largely been borne out by real-world experience and data, it is important for vehicle manufacturers and safety experts to continue monitoring the performance and effectiveness of brake boosting systems and making improvements as needed.
There is a strong causal relationship between the use of brake boosting systems and improved vehicle safety. By amplifying the force applied to the brakes and reducing stopping distances, brake boosters directly contribute to a reduction in accidents and injuries on the road. This causal relationship has been demonstrated through numerous studies and real-world data, which consistently show that vehicles equipped with brake boosting systems are involved in fewer accidents and experience less severe outcomes when accidents do occur.
In addition to this causal relationship, there is also a strong correlation between the adoption of brake boosting systems and overall improvements in vehicle safety. As brake boosting has become more widespread, there has been a corresponding decrease in accident rates and fatalities, even as the number of vehicles on the road has increased. While this correlation does not necessarily prove causation, it does suggest that brake boosting is one of several key factors contributing to the long-term trend of improved vehicle safety.
The mechanism by which brake boosting systems amplify the force applied to the brakes is relatively simple, but highly effective. When the driver presses the brake pedal, the brake booster uses either a vacuum, hydraulic, or electro-hydraulic system to multiply the force applied to the master cylinder. This amplified force is then transmitted to the brake calipers or wheel cylinders, which apply the brakes to the vehicle's wheels.
The specific mechanism of force amplification varies depending on the type of brake booster being used:
In vacuum-assisted systems, the engine's intake manifold creates a vacuum that is used to power the brake booster. When the driver presses the brake pedal, a valve opens and allows air to flow into the booster, which in turn applies force to the master cylinder.
In hydraulic systems, brake fluid is used to transmit force from the brake pedal to the master cylinder. The brake booster uses a hydraulic pump to increase the pressure of the fluid, which amplifies the force applied to the brakes.
In electro-hydraulic systems, an electric motor is used to drive a hydraulic pump, which pressurizes the brake fluid and amplifies the force applied to the brakes. This type of system offers more precise control over the level of force amplification and can be integrated with other electronic safety features.
Regardless of the specific mechanism used, the end result is the same: the force applied by the driver to the brake pedal is multiplied, allowing for shorter stopping distances and improved vehicle control.
While brake boosting is primarily associated with improving safety in passenger vehicles, it also has important applications in the world of racing.
In racing, brake boosting is often used as a technique for building turbo boost pressure before launching the vehicle. This technique, known as "brake boosting" or "boost braking," involves simultaneously pressing the brake and accelerator pedals while the vehicle is stationary or moving slowly. This allows the engine to build up rpm and generate boost pressure without the vehicle accelerating rapidly.
Brake boosting is commonly used in various forms of racing, including drag racing, street racing, and rolling-start races. In these applications, the goal is to generate as much power and acceleration as possible off the starting line, and brake boosting can help achieve this by ensuring that the engine is at peak boost and ready to deliver maximum power as soon as the brakes are released.
While the basic concept of brake boosting is similar in racing and passenger vehicle applications, there are some key differences to note. In racing, the focus is on maximizing power and acceleration, rather than on improving safety or reducing stopping distances. As a result, racing brake boosting systems may be more aggressive and less focused on providing a smooth, progressive braking feel.
Additionally, the specific techniques used for brake boosting in racing, such as holding the brakes while revving the engine, are not applicable or safe for use in passenger vehicles. It is important for drivers to understand the differences between these applications and to use brake boosting systems appropriately based on the specific needs and requirements of their vehicle and driving situation.
In conclusion, brake boosting systems are a vital component of modern vehicle safety, providing drivers with the ability to stop quickly and safely in emergency situations. Through the use of hydraulic, pneumatic, or electro-hydraulic force amplification, brake boosters help to reduce stopping distances, improve vehicle control, and prevent accidents on the road.
As we have seen, brake boosting technology has evolved significantly over the years, and today's systems are more advanced and effective than ever before. From the integration of electronic safety features to the development of regenerative braking in hybrid and electric vehicles, the future of brake boosting is bright and full of potential for even greater improvements in vehicle safety.
However, it is important for drivers to understand the capabilities and limitations of their vehicle's brake boosting system, and to adapt their driving habits accordingly. By staying informed about the latest developments in brake boosting technology and maintaining their vehicle's braking system properly, drivers can help to ensure that they are always ready to stop safely and effectively, no matter what challenges they may face on the road.
Ultimately, the widespread adoption of brake boosting systems in passenger vehicles is a testament to the importance of this technology in enhancing vehicle safety and reducing accidents and fatalities on the road. As we continue to prioritize safety in vehicle design and development, it is clear that brake boosting will remain an essential component of modern automotive engineering for years to come.
The cost of installing a brake boosting system varies depending on the vehicle make, model, and type of booster. On average, expect to pay between $300 to $800 for parts and labor.
Brake boosting systems should be inspected during regular brake maintenance, typically every 30,000 to 50,000 miles. If any issues are detected, the system should be serviced immediately to ensure proper functioning.
Yes, brake boosting systems can be retrofitted to many older vehicles. However, it is essential to ensure that the retrofit kit is compatible with the vehicle's make and model and that the installation is performed by a qualified mechanic.
Brake boosting systems do not directly impact fuel efficiency. However, by providing more effective braking and reducing stopping distances, they can contribute to safer driving practices and potentially reduce the frequency of hard braking, which can improve overall fuel efficiency.
A spongy or unresponsive brake pedal may indicate a problem with the brake boosting system, such as a fluid leak or a faulty master cylinder. If you experience these symptoms, have your braking system inspected by a qualified mechanic as soon as possible.
Yes, brake boosting systems can be integrated with regenerative braking in hybrid and electric vehicles. Electro-hydraulic brake boosters are commonly used in these vehicles to provide seamless integration with the regenerative braking system.
Brake boosting systems enhance vehicle safety by amplifying the force applied to the brakes, resulting in shorter stopping distances and improved braking performance. This is particularly important in emergency braking situations, where quick and effective braking can help avoid accidents or minimize their severity.
When choosing a brake boosting system, consider factors such as vehicle weight, engine size, driving conditions, and personal preferences. Consult with a qualified mechanic or brake specialist to determine the most suitable type of brake booster for your specific vehicle and needs.
Yes, aggressive driving or racing can put excessive strain on brake boosting systems, leading to accelerated wear and potential damage. It is essential to use brake boosting systems responsibly and avoid subjecting them to extreme conditions beyond their designed capabilities.
Future advancements in brake boosting technology may include more sophisticated electronic control systems, improved integration with other vehicle safety features, and the development of lighter, more compact, and efficient boosting mechanisms. These advancements will likely focus on enhancing vehicle safety, performance, and energy efficiency.
Miguel started tinkering with car radios as a teenager, fascinated by the intricate dance of wires and circuits. This passion led him to pursue a career as an automotive electrician. For the past 10 years, Miguel has tackled everything from flickering headlights to mysterious electrical gremlins. He thrives on troubleshooting electrical problems and enjoys sharing his knowledge to empower car owners to understand their vehicles better.
As an automotive mechanic with years of experience, I've encountered countless situations where car owners are puzzled by their vehicle's air conditioning (AC) system. One of the most common questions I receive is, "What should the AC pressure be with the engine off?" This query often arises when drivers notice their AC isn't cooling as effectively as it should, or they suspect a potential issue with the system.
In this article, I'll delve into the intricacies of AC pressure readings, the factors that influence them, and the steps you can take to diagnose and address any underlying problems. Buckle up, as we embark on a journey to demystify this crucial aspect of automotive air conditioning.
Before we dive into the specifics of AC pressure with the engine off, it's essential to grasp the fundamental principles of how an automotive air conditioning system operates. The AC system is a closed-loop circuit that circulates refrigerant, a specialized liquid/gas mixture responsible for absorbing heat from the cabin and expelling it outside the vehicle.
Component | Function |
---|---|
Compressor | Compresses the refrigerant gas, increasing its pressure and temperature |
Condenser | Dissipates heat from the high-pressure, high-temperature refrigerant gas, causing it to condense into a liquid |
Expansion Valve/Orifice Tube | Regulates the flow of refrigerant from the high-pressure side to the low-pressure side |
Evaporator | Absorbs heat from the cabin air, causing the liquid refrigerant to evaporate and cool the air |
The pressure within this closed-loop system is a critical indicator of its overall health and performance. When the engine is running, the AC compressor, driven by the engine, compresses the refrigerant gas, increasing its pressure and temperature. This high-pressure, high-temperature gas then flows through the condenser, where it dissipates heat and condenses back into a liquid state.
However, when the engine is off, the compressor is not actively compressing the refrigerant, and the system should reach a state of equilibrium, where the pressures on both the high and low sides of the system equalize.
In an ideally functioning AC system with no leaks or component failures, the static pressures on both the high and low sides should equalize and match the ambient temperature pressure. This pressure is typically measured in pounds per square inch (PSI) and can be easily determined using a temperature-pressure chart or an AC manifold gauge set.
For example, if the ambient temperature is 75°F (24°C), the static pressure on both sides of the AC system should be around 55-60 PSI when the engine is off. This equilibrium pressure is crucial because it indicates that the system is holding the correct amount of refrigerant and that there are no significant leaks or blockages.
Ambient Temperature | Expected Static Pressure (PSI) |
---|---|
65°F (18°C) | 40-45 PSI |
75°F (24°C) | 55-60 PSI |
85°F (29°C) | 70-75 PSI |
95°F (35°C) | 90-95 PSI |
While an ideal AC system should exhibit balanced pressures when the engine is off, several factors can disrupt this equilibrium, leading to improper pressure readings. Here are some of the most common culprits:
The most prevalent issue causing improper AC pressures is a refrigerant leak within the system. Even small leaks over time can result in low refrigerant levels, which can cause the pressures on both sides to drop below the expected values. Refrigerant leaks can occur due to various reasons, such as:
The compressor is the heart of the AC system, responsible for circulating and compressing the refrigerant. If the compressor fails or becomes faulty, it can disrupt the refrigerant flow and cause uneven or abnormal pressure readings, even with the engine off.
Common signs of compressor failure include:
The expansion valve or orifice tube is a critical component that regulates the flow of refrigerant from the high-pressure side to the low-pressure side of the system. If these components become clogged or obstructed, it can lead to improper pressure readings and inefficient cooling.
Causes of a clogged expansion valve or orifice tube include:
While less common, failures in other AC system components, such as the condenser, evaporator, or receiver/drier, can also contribute to improper pressure readings and overall system performance issues.
If you suspect an issue with your vehicle's AC system due to improper pressure readings with the engine off, it's crucial to have a professional technician diagnose and repair the problem. Here's a general overview of the diagnostic and repair process:
The first step in diagnosing AC pressure issues is to connect an AC manifold gauge set to the service ports on the high and low sides of the system. This specialized tool allows you to monitor the pressures on both sides and identify any discrepancies or abnormalities.
Gauge Set Component | Function |
---|---|
Low-side gauge | Measures the pressure on the low-pressure side of the system |
High-side gauge | Measures the pressure on the high-pressure side of the system |
Manifold | Connects the gauges to the service ports |
Hoses | Allow refrigerant flow between the system and the gauge set |
With the engine off and the AC system at rest, the technician will observe the static pressures on both the high and low sides. If the pressures are low or uneven, it indicates a leak or other system fault that needs further investigation.
If a leak is suspected, the technician will use specialized tools, such as UV dye or electronic leak detectors, to pinpoint the source of the leak. Once identified, the faulty component(s) will be repaired or replaced, and the system will be evacuated and recharged with the correct amount of refrigerant and lubricant.
In cases where a major component, such as the compressor or expansion valve, has failed, replacement of the faulty part is typically required. This process involves evacuating the system, replacing the component, and then recharging the system with the appropriate refrigerant and lubricant levels.
After repairs or component replacements, the AC system will be recharged with the correct amount of refrigerant and lubricant. The technician will then verify the pressures with the engine off to ensure the system is operating within the expected parameters.
While AC pressure issues can be frustrating and costly to repair, there are several proactive measures you can take to prevent or minimize the likelihood of future problems:
Scheduling regular AC system maintenance is crucial for identifying and addressing potential issues before they escalate. During these services, a technician will:
Using your vehicle's AC system regularly, even during cooler months, can help keep the components lubricated and prevent seals from drying out and cracking, which can lead to leaks. It's recommended to run the AC for at least 10-15 minutes every few weeks, even in cooler weather.
While it may be tempting to attempt a DIY recharge with stop-leak additives, these products can often cause more harm than good. They can clog system components and make future repairs more difficult and expensive.
If you notice any signs of AC system issues, such as reduced cooling performance, unusual noises, or visible leaks, it's essential to have the system inspected and repaired promptly. Ignoring these issues can lead to further damage and more costly repairs down the line.
When it comes to AC pressure issues and repairs, it's essential to consider the associated costs. Professional AC diagnosis typically ranges from $100 to $200, while a full recharge service can cost between $150 and $300 on average.
However, if major component replacements are required, such as a new compressor, the costs can escalate significantly, ranging from $500 to $1,000 or more in parts and labor.
Repair/Service | Average Cost Range |
---|---|
AC Diagnosis | $100 - $200 |
Recharge Service | $150 - $300 |
Compressor Replacement | $500 - $1,000+ |
Condenser Replacement | $300 - $800 |
Evaporator Replacement | $400 - $1,000 |
It's important to remember that maintaining your vehicle's AC system proactively is far less expensive than dealing with major repairs down the line. Regular maintenance and addressing issues promptly can save you significant money and hassle in the long run.
Understanding AC pressure readings, particularly with the engine off, is crucial for diagnosing and addressing issues with your vehicle's air conditioning system. By following the guidelines outlined in this article and working with a qualified technician, you can ensure that your AC system operates at optimal efficiency, providing you with a comfortable driving experience.
Remember, proper maintenance and addressing issues promptly are key to preventing costly repairs and ensuring the longevity of your vehicle's AC system. Don't hesitate to seek professional assistance when dealing with AC pressure issues, as attempting DIY repairs without the necessary knowledge and tools can often lead to further complications.
Stay cool, stay informed, and enjoy a refreshing driving experience with a well-maintained and properly functioning air conditioning system.
First, try resetting the furnace circuit breaker. If the fan still doesn't start, you should call a professional HVAC technician for further assistance.
Use a non-conductive tool to short the terminals of the old capacitor before disconnecting any wires. This will safely discharge any residual energy.
It's recommended to replace the AC contactor every five years, even if it appears to be working properly.
If the compressor doesn't run or make any noise when the AC is turned on, it's likely that the compressor has failed and needs to be replaced.
After completing the repairs, reinstall the access panel, turn on the power, and set the thermostat to a lower temperature. The compressor and condenser fan should start running.
If the compressor starts but the fan doesn't spin, the fan motor may be faulty and need to be replaced.
Use a soft brush or vacuum attachment to gently remove any dirt or debris buildup on the evaporator and condenser coils.
Low refrigerant levels can cause the AC to struggle to cool the house effectively or cause the compressor to run continuously without cooling.
Air filters should be changed or cleaned every 1-3 months, depending on usage and the manufacturer's recommendations.
Check the thermostat settings, circuit breakers, and outdoor disconnect to ensure power is reaching the AC unit. If the issue persists, contact a professional for further diagnosis.