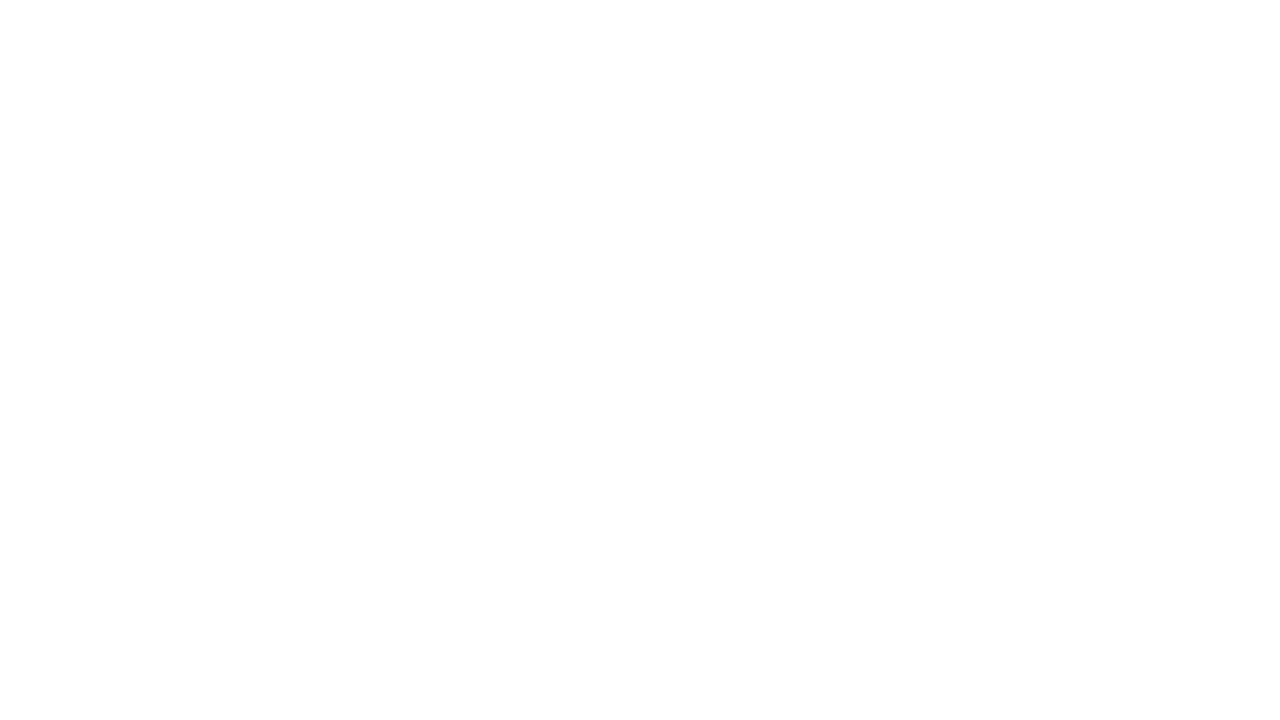
In the relentless pursuit of enhanced performance and efficiency, the automotive industry has embraced a revolutionary technology known as the exhaust turbocharger. This ingenious device harnesses the energy from the engine's exhaust gases, transforming it into a potent force that boosts power output, improves fuel economy, and reduces emissions. Buckle up as we delve into the intricate world of exhaust turbochargers, exploring their working principles, types, installation, applications, and future advancements in this comprehensive guide.
An exhaust turbocharger is a forced induction system that significantly enhances the performance and efficiency of an internal combustion engine. By utilizing the energy from the exhaust gases, a turbocharger can increase the engine's power output, improve fuel efficiency, and reduce emissions. This technology has become increasingly popular in both gasoline and diesel engines, offering a cost-effective way to boost performance without significantly increasing engine displacement.
Benefit | Description |
---|---|
Increased Power Output | Turbochargers compress the air entering the engine's cylinders, resulting in a higher density of air molecules. This increased air density allows for more efficient combustion, generating greater power from the same engine displacement. |
Improved Fuel Efficiency | By compressing the air entering the engine, turbochargers enable the engine to produce more power with less fuel consumption, resulting in better fuel economy. |
Reduced Emissions | The increased air density provided by the turbocharger allows for more complete combustion, resulting in lower levels of harmful emissions such as carbon monoxide, unburned hydrocarbons, and particulate matter. |
At the heart of an exhaust turbocharger are three main components: the turbine, the compressor, and the shaft that connects them. The turbine is driven by the hot exhaust gases from the engine, causing it to spin at high speeds. This spinning motion is the driving force behind the entire turbocharging process.
The compressor is responsible for drawing in ambient air and compressing it before sending it to the engine's intake manifold. As the turbine spins, it transfers its rotational energy to the compressor via the connecting shaft, enabling the compression of the air.
The exhaust turbocharger's working principle revolves around the utilization of exhaust gas energy. As the engine's combustion process takes place, hot exhaust gases are expelled through the exhaust manifold. These gases are directed towards the turbine, causing it to spin at high speeds due to their kinetic energy.
As the turbine spins, it drives the compressor, which draws in ambient air and compresses it. This compressed air has a higher density, containing more oxygen molecules per unit volume. The compressed air is then delivered to the engine's intake manifold, where it is distributed to the cylinders for combustion.
While the fundamental working principle remains the same, exhaust turbochargers come in various types, each designed to cater to specific performance requirements and applications.
Single turbochargers are the most common type, featuring a single turbine and compressor. These turbochargers are widely used in passenger vehicles and light-duty applications due to their simplicity and cost-effectiveness.
Twin-scroll turbochargers have two separate exhaust gas inlets that feed the turbine, allowing for better exhaust gas flow and reduced turbo lag. Turbo lag refers to the delay in power delivery experienced when the turbocharger is spooling up. Twin-scroll turbochargers are often used in high-performance applications where quick response and low-end torque are crucial.
By separating the exhaust pulses from different cylinders, twin-scroll turbochargers can maintain a more consistent flow of exhaust gases to the turbine. This results in faster spool-up times and reduced turbo lag, providing a more immediate power delivery.
Variable Geometry Turbochargers (VGTs) feature adjustable vanes in the turbine housing, which can alter the flow of exhaust gases to optimize performance across a wide range of engine speeds. These turbochargers are commonly found in diesel engines and offer improved efficiency and reduced turbo lag.
The adjustable vanes in the turbine housing of a VGT can change their angle based on the engine's operating conditions. At low engine speeds, the vanes are closed to increase the exhaust gas velocity and improve spool-up time. At higher engine speeds, the vanes open to reduce exhaust gas restriction and prevent over-boosting.
Turbocharger Type | Key Features | Applications |
---|---|---|
Single Turbocharger | Single turbine and compressor, simple and cost-effective | Passenger vehicles, light-duty applications |
Twin-Scroll Turbocharger | Separate exhaust gas inlets, reduced turbo lag | High-performance applications |
Variable Geometry Turbocharger (VGT) | Adjustable turbine vanes, optimized performance across engine speeds | Diesel engines, improved efficiency |
Installing an exhaust turbocharger is a complex process that should be performed by a qualified mechanic or technician. The installation typically involves connecting the turbocharger to the exhaust manifold and intake system, as well as integrating it with the engine's lubrication and cooling systems.
Proper installation is crucial to ensure the turbocharger functions correctly and to prevent potential damage to the engine or the turbocharger itself. Experienced technicians have the knowledge and tools to properly mount the turbocharger, route the necessary piping and hoses, and calibrate the system for optimal performance.
Proper maintenance is crucial for ensuring the longevity and optimal performance of an exhaust turbocharger. Regular oil changes, checking for leaks, and monitoring boost pressure are essential tasks. Additionally, it's important to follow the manufacturer's recommendations for maintenance intervals and procedures.
Regular oil changes: Turbochargers rely on the engine's lubrication system to ensure proper lubrication and cooling. Regular oil changes help prevent the buildup of contaminants and ensure the oil maintains its lubricating properties.
Checking for leaks: Leaks in the turbocharger system can lead to a loss of boost pressure, reduced performance, and potential damage. Regular inspections should be performed to check for leaks in the piping, hoses, and seals.
Monitoring boost pressure: Monitoring the boost pressure can help identify potential issues with the turbocharger system. Abnormal boost pressure readings may indicate a problem with the turbocharger, wastegate, or other components.
Adhering to the manufacturer's recommended maintenance schedule and procedures is essential for maximizing the lifespan and performance of the turbocharger system.
Exhaust turbochargers are widely used in various applications, each with its own unique requirements and challenges.
Both gasoline and diesel-powered passenger cars and SUVs often employ turbochargers to increase power output while maintaining fuel efficiency. Turbochargers allow automakers to downsize engine displacement while still delivering the desired performance, resulting in improved fuel economy and reduced emissions.
In gasoline engines, turbochargers are commonly used in combination with direct fuel injection and advanced engine management systems to optimize power delivery and fuel efficiency. In diesel engines, turbochargers are essential for providing the high levels of boost pressure required for efficient combustion and power output.
Turbochargers are commonly found in trucks, buses, and other commercial vehicles, where they help improve performance and reduce emissions. In these applications, turbochargers play a crucial role in meeting stringent emissions regulations while providing the necessary power and torque for hauling and towing.
Commercial vehicle engines, particularly diesel engines, are often equipped with large turbochargers or multiple turbochargers to handle the high airflow requirements and generate the necessary boost pressure for heavy-duty applications.
Exhaust turbochargers are used in marine engines to boost power and efficiency, particularly in applications where weight and space are limited. The increased power density provided by turbochargers allows for more compact and lightweight engine designs, which is essential in the marine industry.
Marine engines often operate in harsh environments and under demanding conditions, making the reliability and durability of turbochargers a critical factor. Specialized turbochargers designed for marine applications are built to withstand the challenges of saltwater exposure, vibration, and extreme temperatures.
Many industrial machines, such as generators, compressors, and construction equipment, utilize turbochargers to enhance performance and reduce fuel consumption. In these applications, turbochargers contribute to increased productivity, lower operating costs, and improved environmental sustainability.
Industrial engines are often subjected to heavy loads and continuous operation, requiring robust and reliable turbocharger systems. Turbochargers used in industrial applications are designed to withstand extreme operating conditions, such as high temperatures, dust, and vibration.
Application | Key Requirements | Turbocharger Considerations |
---|---|---|
Passenger Vehicles | Fuel efficiency, emissions reduction, performance | Downsized engines, advanced engine management systems |
Commercial Vehicles | Power and torque for hauling and towing, emissions compliance | Large turbochargers, multiple turbochargers |
Marine Engines | Compact and lightweight designs, reliability, durability | Specialized marine turbochargers, saltwater resistance |
Industrial Machinery | Robust and reliable operation, heavy-duty applications | Extreme operating condition tolerance, continuous operation |
The field of exhaust turbocharging is constantly evolving, with manufacturers and researchers exploring new technologies and materials to improve performance, efficiency, and reliability.
Variable Geometry Turbines (VGTs) are an advanced form of turbochargers that can adjust their geometry to optimize performance across a wide range of engine speeds. These turbines can reduce turbo lag and improve efficiency by precisely controlling the flow of exhaust gases through the turbine.
The adjustable vanes in the turbine housing of a VGT can change their angle based on the engine's operating conditions. At low engine speeds, the vanes are closed to increase the exhaust gas velocity and improve spool-up time. At higher engine speeds, the vanes open to reduce exhaust gas restriction and prevent over-boosting.
The use of lightweight and heat-resistant materials, such as ceramics and advanced alloys, is enabling the development of more durable and efficient turbochargers. These materials can withstand the extreme temperatures and stresses associated with turbocharging, leading to improved reliability and longevity.
Ceramic turbine wheels, for example, are lighter and more resistant to thermal shock than traditional metallic turbine wheels. This allows for faster spool-up times and improved efficiency. Advanced alloys, such as nickel-based superalloys, are used in turbine housings and other components to withstand the high temperatures and pressures encountered in turbocharging applications.
The integration of electric motors and energy recovery systems, as seen in e-turbos (electric turbochargers), is a promising trend that could further enhance turbocharger performance and efficiency. E-turbos use an electric motor to assist the turbine in spinning the compressor, virtually eliminating turbo lag and improving low-end torque.
In an e-turbo system, the electric motor is powered by a battery or an energy recovery system that captures energy from the exhaust gases or other sources. This additional power boost from the electric motor can help overcome the initial inertia of the turbocharger, resulting in faster spool-up times and improved transient response.
Advanced simulation and modeling techniques, such as Computational Fluid Dynamics (CFD), are being used to optimize turbocharger designs and improve overall performance. CFD allows engineers to analyze and visualize the complex flow patterns within turbochargers, enabling them to make informed design decisions and refine the aerodynamics for maximum efficiency.
By simulating the flow of exhaust gases through the turbine and the flow of air through the compressor, CFD can identify areas of turbulence, flow separation, and other inefficiencies. This information can then be used to optimize the shape and geometry of the turbine and compressor components, as well as the internal flow paths, to reduce losses and improve overall efficiency.
Advancement | Description | Benefits |
---|---|---|
Variable Geometry Turbines | Adjustable turbine vanes optimize performance across engine speeds | Reduced turbo lag, improved efficiency |
Advanced Materials | Lightweight and heat-resistant materials like ceramics and advanced alloys | Increased durability, faster spool-up, improved efficiency |
Electrification (e-turbos) | Electric motor assists turbine, powered by energy recovery systems | Eliminated turbo lag, improved low-end torque |
Computational Fluid Dynamics (CFD) | Simulations and modeling optimize turbocharger designs | Reduced losses, improved aerodynamics, increased efficiency |
Exhaust turbochargers have revolutionized the automotive industry by offering a cost-effective way to increase engine power output while improving fuel efficiency and reducing emissions. From passenger vehicles to commercial and industrial applications, turbochargers have become an integral part of modern engine design. As technology continues to advance, we can expect to see further innovations in turbocharger design, materials, and integration with other systems. The future of exhaust turbochargers promises even greater performance, efficiency, and reliability, making them an essential component in the pursuit of sustainable and powerful engines.
A turbocharger is a forced induction device that increases the power output of an internal combustion engine by compressing the air entering the cylinders. It utilizes the exhaust gases to drive a turbine that powers the compressor.
By compressing the air entering the engine, turbochargers allow for more efficient combustion, resulting in increased power output from a smaller engine displacement. This leads to better fuel economy compared to larger naturally aspirated engines.
Turbo lag refers to the delay in power delivery when the turbocharger is spooling up. It is caused by the inertia of the turbo components and the time required for the exhaust gases to accelerate the turbine.
A single-turbo setup uses one turbocharger, while a twin-turbo setup employs two turbochargers, either for separate cylinder banks or for different RPM ranges. Twin-turbos offer a broader power band but are more complex and expensive.
A twin-scroll turbocharger has a divided turbine housing that separates the exhaust gas flow from different cylinders, resulting in more efficient delivery of exhaust energy to the turbine and improved response.
VGTs have adjustable vanes in the turbine housing that can alter the flow of exhaust gases, optimizing performance across a wide range of engine speeds and reducing turbo lag.
Electric turbochargers use an electric motor to assist the turbine, virtually eliminating turbo lag and improving low-end torque. They can also recover energy from the exhaust gases or other sources.
Adding a turbocharger increases the mechanical complexity of the engine, potentially leading to more maintenance requirements and a higher risk of failure if not properly maintained or installed.
Proper maintenance, such as regular oil changes, checking for leaks, and monitoring boost pressure, is crucial for ensuring the longevity and optimal performance of a turbocharger.
Yes, turbochargers are widely used in various applications, including passenger vehicles, commercial vehicles, marine engines, and industrial machinery, each with its own unique requirements and challenges.
Sarah isn't your average gearhead. With a double major in Mechanical Engineering and Automotive Technology, she dived straight into the world of car repair. After 15 years of turning wrenches at dealerships and independent shops, Sarah joined MICDOT to share her expertise and passion for making cars run like new. Her in-depth knowledge and knack for explaining complex issues in simple terms make her a valuable asset to our team.