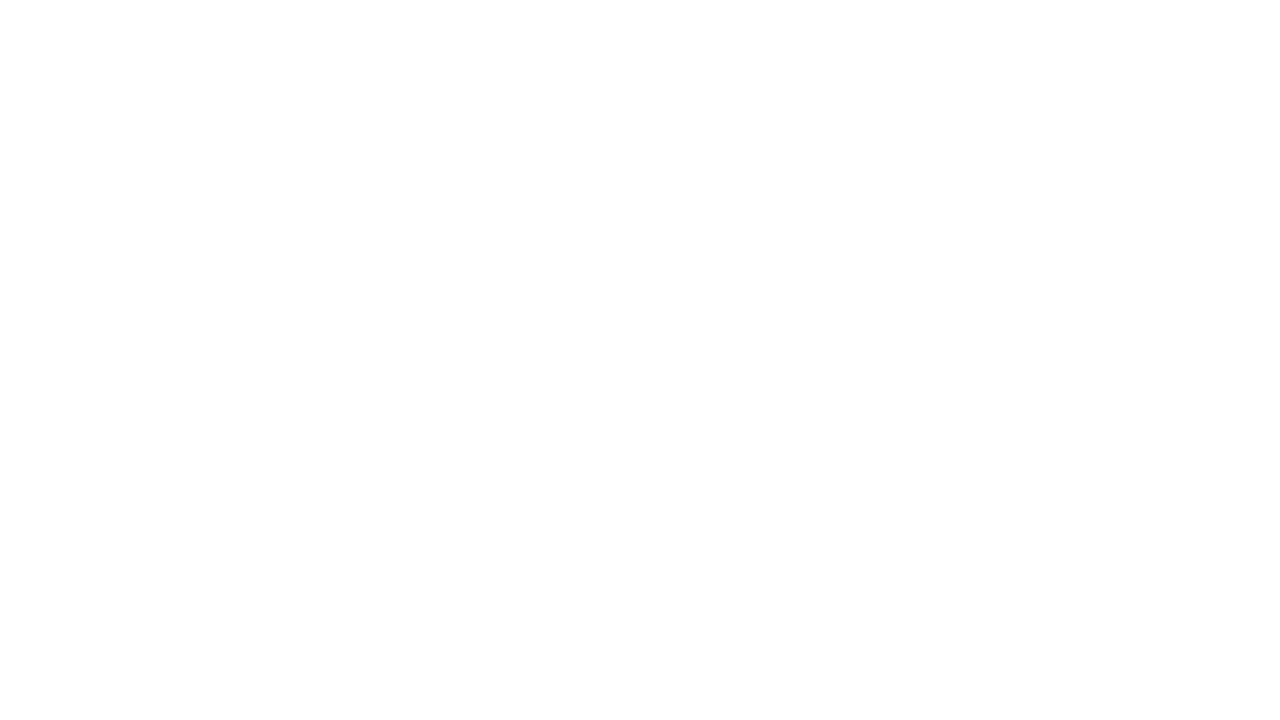
In the ever-evolving automotive industry, valves play a pivotal role in regulating and controlling the flow of various fluids, gases, and air-fuel mixtures. From engine components to braking systems, these mechanical marvels ensure efficient and reliable performance. This comprehensive guide delves into the intricate world of valves, exploring their types, components, materials, applications, selection criteria, maintenance practices, and emerging trends. By understanding the intricacies of valve technology, automotive professionals and enthusiasts can optimize vehicle performance, enhance safety, and stay ahead of the curve.
Valves are mechanical devices designed to regulate, direct, or control the flow of fluids, gases, or fluidized solids within a system. They are essential components in piping systems and are widely used across various industries, including the automotive sector, where they play a critical role in controlling the flow of air, fuel, coolant, and other fluids within the vehicle's systems, ensuring proper engine operation, efficient braking, and optimal performance.
The automotive industry utilizes several types of valves, each designed to serve specific functions and applications. Understanding the different valve types is essential for proper selection and implementation.
Valve Type | Description | Automotive Applications |
---|---|---|
Ball Valves | Quarter-turn valves that use a rotating ball with a bore to control the flow. Suitable for on/off applications and can handle high pressures and corrosive fluids. | Fuel delivery systems, cooling systems |
Gate Valves | Use a sliding gate or wedge to start or stop the flow. Commonly used for on/off applications and can handle high temperatures and pressures. | Cooling systems, hydraulic systems |
Globe Valves | Use a movable disk or plug to regulate the flow. Suitable for throttling applications and can provide precise flow control. | Fuel delivery systems, cooling systems (precise flow regulation) |
Butterfly Valves | Use a rotating disc or vane to control the flow. Compact and suitable for large-diameter piping systems. | Air intake systems, exhaust systems |
Check Valves | Allow flow in one direction and prevent backflow. Self-actuating and used to protect equipment from reverse flow. | Fuel delivery systems, cooling systems, hydraulic systems (prevent backflow) |
Valves are composed of several essential components that work together to regulate the flow of fluids or gases. Understanding these components is crucial for proper valve selection, operation, and maintenance.
The valve body is the primary pressure boundary that holds the valve components and connects to the piping system. It is designed to withstand the operating pressures and temperatures of the system.
The bonnet is a removable component that provides access to the valve's internal parts, allowing for maintenance, inspection, and replacement of internal components when necessary.
The valve trim refers to the internal components that directly control the flow of fluids or gases. It typically includes:
Disk or Plug: The movable component that opens or closes the valve's flow path, determining the valve's flow characteristics and performance.
Seat: The stationary component against which the disk or plug seals to control the flow, designed to provide a tight seal and prevent leakage when the valve is closed.
Stem: The component that connects the disk or plug to the actuator, transmitting the force from the actuator to the trim, allowing the valve to open or close.
The actuator is the mechanism that operates the valve, either manually or automatically. Automotive valves may employ different types of actuators:
Manual: Require human intervention to open or close the valve, commonly used in applications where frequent adjustments are not required.
Pneumatic: Use compressed air to operate the valve, suitable for applications where remote or automatic control is necessary.
Electric: Use electric motors or solenoids to open and close the valve, often used in applications that require precise control and automation.
Hydraulic: Use pressurized hydraulic fluid to operate the valve, commonly found in high-pressure applications and heavy-duty systems.
The packing is a sealing component that prevents leakage around the stem where it passes through the valve body. It is designed to maintain a tight seal while allowing the stem to move freely during valve operation.
Valves can be constructed from various materials, depending on the operating conditions, fluid properties, and environmental factors. The selection of appropriate materials is crucial for ensuring corrosion resistance, temperature and pressure tolerance, and overall durability.
Material | Description | Advantages | Limitations |
---|---|---|---|
Carbon Steel | Common material used in valve construction, offering good strength and durability. | Suitable for moderate temperatures and pressures, cost-effective. | Limited corrosion resistance. |
Stainless Steel | Popular choice due to excellent corrosion resistance and durability. | Suitable for harsh environments or corrosive fluids, high strength. | Higher cost compared to carbon steel. |
Cast Iron | Cost-effective material used in low-pressure applications. | Good strength and wear resistance. | Susceptible to corrosion in certain environments. |
Alloys | Nickel-based or chromium-based alloys used when superior corrosion resistance, high-temperature tolerance, or specific material properties are required. | Excellent corrosion resistance, high-temperature tolerance, tailored properties. | Higher cost compared to other materials. |
The selection of valve materials is based on various factors, including operating temperatures and pressures, fluid properties (corrosiveness, abrasiveness, viscosity), environmental conditions (humidity, exposure to chemicals), cost considerations, and industry standards and regulations.
Valve design, construction, and performance are governed by industry standards and specifications to ensure safety, reliability, and interoperability across different systems and applications.
API Standards: The American Petroleum Institute (API) standards are widely recognized in the automotive industry and cover various aspects of valve design, testing, and performance.
ASME Standards: The American Society of Mechanical Engineers (ASME) standards provide guidelines for valve design, materials, and testing procedures, ensuring compliance with safety and performance requirements.
ISO Standards: The International Organization for Standardization (ISO) standards are globally recognized and cover various aspects of valve design, construction, and performance, promoting consistency and interoperability across different regions and industries.
Adhering to industry standards and specifications is crucial for ensuring the safety, reliability, and compatibility of valves used in automotive applications. Compliance with these standards helps manufacturers and end-users mitigate risks, improve performance, and meet regulatory requirements.
Valves are employed in various automotive systems and components, playing a vital role in regulating and controlling the flow of fluids, gases, and air-fuel mixtures.
Valves are essential components in engine systems, including:
Intake and Exhaust Valves: Control the flow of air and exhaust gases in the engine cylinders, enabling the combustion process and engine operation.
Fuel Delivery Valves: Regulate the flow of fuel to the engine, ensuring proper air-fuel mixture and efficient combustion.
Cooling System Valves: Control the flow of coolant, helping to maintain optimal engine temperatures and prevent overheating.
Valves play a crucial role in automotive braking systems:
Brake Valves: Control the flow of hydraulic fluid in the braking system, enabling the application of braking force to the wheels.
Anti-lock Braking System (ABS) Valves: Modulate the brake pressure to prevent wheel lockup and maintain vehicle stability during braking.
Valves are used in transmission systems to regulate the flow of hydraulic fluid, enabling smooth gear shifts and efficient power transfer.
Heating, ventilation, and air conditioning (HVAC) systems in vehicles employ valves to control the flow of refrigerant and air, ensuring proper cabin temperature and air quality.
Valves are used in emission control systems, such as exhaust gas recirculation (EGR) systems, to regulate the flow of exhaust gases and reduce harmful emissions.
Selecting the appropriate valve type and size is crucial for ensuring proper system performance, efficiency, and reliability in automotive applications.
The properties of the fluid or gas being controlled, such as viscosity, temperature, and corrosiveness, play a significant role in valve selection. Valves must be compatible with the fluid properties to prevent premature wear, corrosion, or failure.
The required flow rate of the fluid or gas determines the valve size and capacity. Undersized valves can lead to excessive pressure drop and reduced system performance, while oversized valves may result in poor control and inefficient operation.
Operating conditions, such as pressure, temperature, and environmental factors, must be considered when selecting valves. Valves must be rated for the specific operating conditions to ensure reliable performance and prevent failure.
Proper valve sizing involves calculating the required flow coefficients and pressure drop to determine the appropriate valve size and trim characteristics. These calculations take into account factors such as flow rate, fluid properties, and system operating conditions.
The flow coefficient (Cv) is a measure of a valve's ability to allow fluid flow. It is used to determine the valve size required to achieve the desired flow rate while minimizing pressure drop.
Pressure drop is the difference in pressure across a valve when it is in the open position. Calculating the pressure drop is essential for ensuring that the valve does not cause excessive pressure losses or restrict flow in the system.
Regular maintenance and troubleshooting are essential for ensuring the proper functioning and longevity of valves in automotive applications.
Preventive maintenance tasks help to identify and address potential issues before they lead to valve failure or system downtime.
Lubricating moving parts, such as stems and actuators, is crucial for reducing friction and wear, ensuring smooth operation, and prolonging valve life.
Inspecting seals and gaskets for signs of wear, damage, or leakage is essential to prevent fluid leaks and maintain proper valve performance.
Regular leak detection and monitoring can help identify and address leaks early, preventing potential system failures and environmental concerns.
Despite regular maintenance, valves may encounter various issues that require troubleshooting and corrective actions.
Sticking valves can be caused by debris, corrosion, or lack of lubrication, while leaking valves may result from worn seals, gaskets, or improper installation.
Exposure to harsh environments or corrosive fluids can lead to erosion and corrosion of valve components, compromising their performance and integrity.
Issues with actuators, such as pneumatic or electric failures, can prevent valves from opening or closing correctly, leading to system malfunctions.
Proper troubleshooting techniques, such as visual inspections, leak testing, and actuator diagnostics, can help identify the root cause of valve issues and guide appropriate corrective actions.
The valve industry is continuously evolving, with new trends and innovations aimed at improving efficiency, safety, and performance in automotive applications.
The integration of sensors, communication technologies, and advanced control systems enables the development of smart valves. These valves can provide real-time monitoring, predictive maintenance, and automated operation, improving system performance and reducing downtime.
The development of new materials and coatings, such as high-performance alloys and composites, enhances corrosion resistance, durability, and performance in extreme operating conditions. These advanced materials can extend the service life of valves and improve their reliability in demanding automotive applications.
Manufacturers are focusing on developing energy-efficient valve designs that reduce energy consumption and improve sustainability. These designs may include optimized flow paths, low-power actuators, and intelligent flow control algorithms, contributing to improved fuel efficiency and reduced emissions.
As automotive systems become more compact and space-constrained, there is a growing demand for compact and space-efficient valve solutions. Manufacturers are exploring innovative designs and materials to create smaller, lighter, and more compact valves without compromising performance or reliability.
Valves are essential components in the automotive industry, playing a vital role in regulating and controlling the flow of fluids, gases, and air-fuel mixtures. By understanding the types, components, materials, and applications of valves, automotive professionals and enthusiasts can make informed decisions regarding valve selection, maintenance, and troubleshooting.
Proper valve selection and sizing are crucial for ensuring optimal system performance, efficiency, and reliability. Regular maintenance and timely troubleshooting can prevent valve failures, extend service life, and minimize downtime.
As the automotive industry continues to evolve, new trends and innovations in valve technology, such as smart valves, advanced materials, energy-efficient designs, and compact solutions, will further enhance performance, safety, and sustainability.
By staying informed about the latest developments in valve technology and adhering to industry standards and best practices, automotive professionals can ensure that their vehicles operate at peak performance while meeting stringent safety and environmental regulations.
The key factors include corrosion resistance, temperature limitations, pressure ratings, fluid compatibility, mechanical strength, and manufacturing feasibility.
Valve actuators operate the valve either manually, pneumatically, electrically, or hydraulically, allowing for remote or automatic control.
Valve trim components like the disk/plug, seat, and stem directly control and regulate the flow of fluids or gases through the valve.
Proper valve sizing ensures efficient flow control, minimizes pressure drops, and maximizes the valve's lifespan and system performance.
Common maintenance tasks include lubrication, seal and gasket inspection, and leak detection to prevent valve failure and system downtime.
Smart valves integrate sensors, communication technologies, and advanced control systems, enabling real-time monitoring, predictive maintenance, and automated operation.
Valve standards and specifications, such as those from API, ASME, and ISO, ensure safety, reliability, interoperability, and compliance with industry requirements.
Advanced materials and coatings, like high-performance alloys and composites, offer improved corrosion resistance, durability, and performance in extreme conditions.
Energy-efficient valve designs reduce energy consumption, improve fuel efficiency, and contribute to sustainability by optimizing flow paths and utilizing low-power actuators.
As automotive systems become more compact, there is a growing demand for smaller, lighter, and more space-efficient valve solutions without compromising performance.
Sarah isn't your average gearhead. With a double major in Mechanical Engineering and Automotive Technology, she dived straight into the world of car repair. After 15 years of turning wrenches at dealerships and independent shops, Sarah joined MICDOT to share her expertise and passion for making cars run like new. Her in-depth knowledge and knack for explaining complex issues in simple terms make her a valuable asset to our team.